來源:電源技術
作者:楊朝蓬,張寧,段志宇
摘要:鋰離子電池作為電動汽車動力電池首選,維持其工作在最佳溫度范圍需要應用散熱系統。針對常用的風冷散熱系統,闡述了不同類型的特點,綜述了國內外在電池內部流道、進出風口結構、冷卻空氣流體參數等方面開展的仿真與實驗研究,以及采用優化算法和優化策略,改善電池內部溫度和溫差的優化設計研究。為克服風冷散熱系統冷卻效率低及密封性不足的問題,基于風冷散熱系統的混合冷卻系統被研究者廣泛提出。
關鍵詞:鋰離子電池;風冷散熱系統;溫度;溫差;混合冷卻系統
隨著環境污染與能源緊缺問題加劇,世界各國加大了電動汽車的研發力度,而動力電池作為電動汽車的動力來源,受到各國政府和主要汽車制造廠商的重點關注。鋰離子電池具有比能量高、循環壽命長、自放電率低、無污染排放等特點,成為目前電動汽車首選的動力電池體系。鋰離子動力電池的性能和壽命在很大程度上與工作溫度有關,通常最佳工作溫度在 15~40℃,溫差低于 5℃。在充放電過程中電池自身產熱會導致溫度上升,適當的散熱冷卻技術可以減少溫度對電池組的負面影響,提高動力電池的效率和安全性,降低老化率,延長使用壽命。車用鋰離子動力電池散熱系統冷卻方式主要有:風冷、液冷、相變材料(PCM)冷卻、熱管(HP)冷卻等。風冷、液冷是應用最廣泛的冷卻方式,受技術水平限制,當前國內主要采用風冷,有少數電動車也開始采用系統更為復雜的液冷,如吉利帝豪 EV、江淮 iEV7S,而國外發達國家更多采用液冷,如美國特斯拉、雪佛蘭沃藍達。作為新型冷卻方式,相變材料和熱管冷卻還處于研究和小規模應用階段。本文介紹了車用鋰離子動力電池風冷散熱系統的主要類型及特點,綜述了近幾年國內外關于風冷散熱系統的應用及研究進展。
01 風冷散熱系統特點
風冷散熱系統具有結構簡單、質量輕巧、成本低,無有害氣體積壓和漏液風險,但不足之處是散熱效率低,密封設計難度大,防塵、防水效果差。根據冷卻風源是否使用額外裝置引入,風冷散熱系統分為自然風冷和強制風冷。將車輛行駛過程中產生的迎風風流經導流管導入電池組內部通道進行直接冷卻的方式叫做自然風冷。該方式不需要輔助電機、結構簡單、使用方便,但冷卻氣流會因車速變化而不穩定,冷卻效果差異較大,而且空氣的熱容和熱導率都很低,自然對流表面換熱系數小。自然風冷適合應用于動力電池放電倍率小、產熱率低的汽車,如比亞迪在秦、唐、宋、E6、騰勢等采用磷酸鐵鋰電芯的車型上都采用了自然風冷。限于電池組成本、整車續航里程以及零部件體系等因素,國內大部分300 km續航里程以下的純電動車目前大都選用自然風冷。以消耗電池能量為代價,利用風扇或者空氣泵來促進空氣流動,形成強制對流來強化傳熱的方式叫做強制風冷。該方式能夠提供穩定的冷卻氣流,但結構相對復雜。自然風冷一般要求動力電池本身發熱量小,且布置空間的空氣流動順暢,國內目前的電池制造能力還達不到該水平,故強制風冷是國內主流的風冷散熱類型。強制風冷在國外早期的電動乘用車上應用廣泛,如日本豐田 Prius、本田 Insight、日產聆風、通用 Volt、起亞 Soul EV 等,在國外的電動巴士、電動物流車中也被廣泛應用。根據空氣來源不同,強制風冷散熱系統可分為環境風冷卻和空調風冷卻。動力電池多安裝于車輛地板下方,環境風冷卻因絕緣故障等因素未見批量生產車型中。因此,強制風冷多指空調風冷卻,根據空調風來源不同,又分為兩種形式:(1)艙內引風式:環境空氣經整車空調冷卻之后進入乘員艙,隨后由乘員艙通入動力電池內,最后由風扇將其排入到環境中。國內大多數汽車企業采用該方式,如江淮 iEV4、上汽榮威 MARVEL X。(2)獨立風冷式:環境空氣經電池系統自身空調冷卻后直接引入,散熱效率相對較高,也避免了風量需求大時乘員艙出現負壓感受,但相應增加了成本和能耗,美國CODA 公司與長安哈飛合作的長安E30采用了該方式。
02 風冷散熱系統研究進展
針對自然風冷和強制風冷散熱系統,國內外研究主要基于計算流體動力學(CFD)分析電池內部流道、進出口結構、冷卻空氣流體參數等因素對電池組整體溫度值高低及溫度均勻性的影響規律,采用優化策略對風冷散熱系統參數進行優化設計,以期望獲得更好的系統散熱效率,改善電池組溫度場分布。在電池內部,單體或模組因排布形式不同而形成不同的流道結構。根據空氣在流道內的流通方式,電池內部的冷卻模式主要分為串行風冷和并行風冷。如圖1所示,串行風冷時冷卻空氣從電池一側通入,依次流經各個單體。如圖2所示,并行風冷時冷卻空氣均勻流經并列排布的單體間隙。相比于并行風冷,串行風冷下冷卻空氣在流動過程中逐漸被加熱,與單體的溫差逐漸減小,對流換熱能力下降,靠近出口側的單體散熱效果比進口側差,溫度分布均勻性較差。并行風冷需要對進、出口處流道結構進行特殊設計,滿足不同位置處的進風量和壓力角度,從而保證流場分布均勻性,因此結構相對復雜。一般情況下,串行風冷多適用于采用圓柱單體的動力電池,并行風冷多適用于采用方形單體的動力電池。
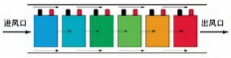
圖1 串行風冷圖
為了改善串行風冷和并行風冷模式下的散熱效率和散熱均勻性,在流道設計方面,可通過改變單體的排布方式或排布間距來實現。串行風冷下常用的排布方式如圖3所示,主要包括平行順排、交叉排列、錯位排列、梯形叉排等。并行風冷下常用的排布方式如圖4所示,主要包括行排列和列排列。
對于不同排布方式、排布間距的影響結果,針對具體應用場景開展了眾多研究。李康靖等對 18650 圓柱鋰離子動力電池包2C放電時的溫度場進行了仿真分析,發現順排比叉排、錯排散熱效果要好,減小順排單體間距可抑制最高溫度,但會消減溫度均勻性。張繼華等運用COMSOL仿真平臺計算了21700圓柱鋰離子電池組5C充放電溫度場分布,得出交叉排列比平行排列的最高溫度更低、溫差更小,隨著單體間距的加大,電池組最高溫度降低。彭睿等對比平行順排和梯形叉排兩種散熱方案,發現梯形叉排散熱方案上游和中游處最高溫度下降更多、散熱均勻性更好,但下游處因排布間距小、熱量積聚,下表面散熱效果不如平行順排。張鑫等運用FLUENT仿真軟件分析了方形鋰電池并行風冷溫度場分布,發現列排列單體的溫度和溫差整體上低于行排列。因此,在散熱系統設計時,應根據所選電芯種類、放電功率、電池包結構尺寸來確定單體排布方式、排布間距。風冷散熱系統的進出風口位置、尺寸、形式,直接決定了進入電池組內部的冷卻空氣流動方向和風量,對內部流場分布具有較大影響,會影響散熱效果。Xu 等研究發現自然風冷下帶通風口的電池組比不帶通風口的最大溫升和最大溫差分別降低了約23.1%和19.9%。Yang 等利用速度場與溫度梯度場協同原理分析發現電池組上出風模式具有最佳的冷卻效果,當進氣量為 0.444 m/s 時,最大溫升和最大熱源溫差可控制在7.01和3.08 ℃。E 等研究表明位于不同側的進出口冷卻性能優于相同側。張新強等采用數值模擬發現當通風孔與出風口面積相等時,電池組冷卻效果最佳,繼續增大通風孔面積,并不能明顯提高電池組的冷卻效果。王天波等研究發現在進出口面積不變的情況下,進出口形狀為圓形時,散熱效果最佳。徐輝發明了若干與電池模塊內部貫通的喇叭狀收風器,收風器大口均朝向車輛行駛方向,保證自然風冷下不同電池模塊具有較為對等的進風量,減少模塊間散熱差異。蘭海俠等在空氣出入口流道上分設傾斜的分流板,提高了并行風冷下散熱效果。為了改善串行風冷下冷卻空氣依次流動導致溫度分布不均勻的問題,可以通過控制進出口動作來改變內部空氣流動模式,擾動流場,提升散熱均勻性。如圖5(a)所示,袁征等在電池一側設置一個進風口,另一側設置兩個出風口,通過控制兩個出風口開關閥門交替開啟或關閉,實現空氣在電池箱體中變向循環流動;如圖5(b)所示,馬永笠等提出了一種使用進出口鼓風機交替工作實現電池組內部空氣往復流動的方案,該方案下電池組整體溫度保持在 25~45℃,最大溫差控制在指定溫度;如圖5(c)所示,宋俊杰等提出了反向分層風冷結構,該結構下各電池溫度分布非常均勻。

圖5 冷卻空氣流動模式
冷卻空氣流體參數主要包括冷卻空氣溫度和入口風速,這兩個參數對風冷散熱系統的散熱效率和散熱均勻性也有著明顯影響。汪繽繽等通過對48只圓柱鋰離子電池組成的電池包進行風冷散熱研究,發現隨著入口風速的增加,電池包的最高溫度和最大溫差降低,但當入口風速大于3 m/s后,最高溫度和最大溫差降低速度明顯減小;降低入口冷卻空氣溫度,可以降低電池包最高溫度,但對電池包的溫差影響很小。劉顯茜等通過三維瞬態計算,發現增大入口風速可提升電池組散熱性能,改善溫度均勻性,降低進風溫度可防止電池組因局部溫度過高而出現熱失控,但無法有效抑制溫度均勻性。冷卻空氣溫度由風源決定,若風源為環境風則冷卻空氣溫度與環境溫度一致,若風源為空調風則可根據需要設定不同的冷卻空氣溫度。冷卻空氣的入口風速由風冷散熱系統中的風機決定,而風機選型是根據電池的產熱速率確定空氣流量,然后根據所需空氣流量和電池組的流道阻力情況,從具有合適壓力-流量曲線(P-Q 曲線)的風機中選出。風冷散熱系統的散熱效率和散熱均勻性與電池組內部的排布方式、排布間距,進出風口位置、尺寸、形式,進風方向、風速、溫度等參數密切相關,這些參數會共同影響電池內部的溫度場分布狀態。可以采用相應的優化策略或優化算法,獲得合適的系統參數,以達到可以接受的最佳風冷散熱效果。白帆飛等運用正交實驗法對電池組間距遞減幅度、上集流板傾斜角度、下集流板傾斜角度等結構參數進行了優化設計,確定了最優結構:間距遞減幅度0.3 mm、上集流板傾斜0°、下集流板傾斜 5°。李淼林等基于正交實驗進行多目標優化,將電池組最高溫度和溫差最小化作為目標,經多次迭代計算,得出局部優化方案:進風區域左端高度 9 mm(進風角度 2.74°),出風口高度 28 mm(出風角度 2°),電池間距公差值為 0.4 mm。與優化前相比,電池組最高溫度降低了 9.55%,溫差下降 25.89%。夏博妍采用窮舉法和遺傳算法對風冷式熱管理系統的進、出風口導流板角度和電池排布間距進行了優化設計,優化后充、放電狀態下最高溫度分別由37.5、43.5℃下降到33.8、37.3℃,電池單體最大溫差分別由6.0、9.9℃下降到1.1、1.7℃。Xie等借助實驗和計算流體力學,采用單因素分析和正交實驗法對進氣角、出氣角、電池單元之間的氣流通道寬度三個結構參數進行了優化,在 2.5°進氣角、2.5°排氣角和相等的通道寬度條件下冷卻性能最佳。Chen 等開發了流動阻力網絡模型,使用嵌套循環程序和計算方法優化了氣室的角度以及入口和出口的寬度,優化結果顯示,優化氣室角度不能有效降低電池單元之間的溫度和溫差,而優化進口和出口的寬度可以顯著提高冷卻效率。
03 風冷散熱系統的耦合應用
風冷散熱效率低,但結構簡單、成本低。為充分發揮風冷散熱系統的優勢,同時應對風冷散熱系統散熱效率已逐漸無法滿足電動汽車功率、里程的發展需求,將風冷與液冷、PCM冷卻、HP 冷卻等方式耦合應用,形成混合冷卻系統,逐漸成為國內外動力電池熱管理系統發展的一種趨勢。如圖6所示,徐曉明等發明了一種風冷與液冷耦合應用的電池模組,在模組底部設置了液冷板,電芯之間設置了風冷空腔,單體電池裝在閥口與風冷空腔連通的套筒內,控制系統根據溫度傳感器測量值,選擇性控制液冷板和風冷系統動作,保證最佳工作溫度范圍。如圖7所示,Qin 等提出了一種風冷與 PCM 冷卻耦合應用的電池模組,將石蠟作為PCM,填充在單體電池四周的鋁合金管中,冷卻空氣在鋁合金管形成的框架結構中流動。如圖8所示,Behi 等提出了一種風冷與熱管冷卻耦合應用的電池模塊,經仿真計算,采用強制風冷、增加熱管(HP)和增加帶有銅片的熱管(HPCS)三種冷卻策略,與自然風冷相比,電池模塊最高溫度可降低34.5%、42.1%、42.7%,溫度均勻性提高 39.2%、66.5%、73.4%,溫度均勻性提升明顯。
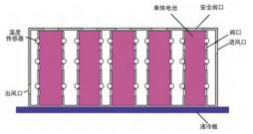
圖8 風冷與熱管耦合冷卻
如圖9所示,饒中浩等將風冷與 PCM 冷卻、熱管冷卻三種冷卻方式有機結合,PCM 直接填充于單體電池與模塊外壁之間,用于直接吸收電池熱量,熱管蒸發端直接插入模塊底部 PCM 內,吸收其中熱量,施加于外部翅片和模塊中心流道的冷卻空氣同時冷卻熱管冷凝端、PCM 和單體電池。如圖10 所示,Wei 等提出了將風冷、液冷和 PCM 三種方式耦合冷卻的概念,纖維通道內流動的水作為液冷介質,同時作為PCM,在重力和纖維薄壁毛細作用下受熱蒸發,蒸發形成的水蒸氣在冷卻空氣的流動作用下帶走電池潛熱,經測試表明,相比無冷卻、僅風冷和僅水冷,該混合冷卻方法使電池包最高表面溫度降低了約 83%、70% 和 57%,并成功地將溫度均勻性保持在建議的 5 ℃以下。將冷卻空氣引入電池內部進行直接風冷會降低電池組密封性能,密封性能低可能會導致絕緣故障,為解決這一問題,將風冷方式與整套熱交換系統耦合,由熱交換系統將電池內部的熱量導出,最終冷卻空氣在電池殼體外部實現散熱冷卻。Park 等將熱交換系統管路圍繞在電池組殼體外側,熱交換系統包含進氣口、出氣口、預定流動通道,通過風扇和熱電元件控制冷卻空氣進入熱交換系統的流動通道,從而將電池導出的潛熱散出。Mardall 等將熱交換器管道機械地和熱地耦合到電池組外殼基板的內表面,電池組外殼外表面上流動的冷卻空氣將熱交換系統中的熱分離。
04 總結與展望
相比于低散熱效率的自然風冷,強制風冷是風冷散熱系統中的主流冷卻方式。風冷散熱系統的散熱效率與電池組內部排布結構、進出風口設置、冷卻空氣流體參數等因素密切相關。通過采用優化策略和優化算法,以評判電池內部溫度水平和溫度均勻性的指標作為優化目標,對各類結構與控制參數進行優化設計,可有效提升風冷散熱系統的散熱效果。電動汽車的發展,對鋰離子動力電池的功率和車輛的續航里程提出了更高的要求,動力電池的能量密度、功率密度將逐漸增大,電池自身的發熱量和發熱功率也將隨之增大。盡管風冷散熱系統通過優化設計,散熱效率可以得到提升,但是空氣自身低熱容量、低導熱系數從本質上決定了優化提升空間有限。因此,風冷散熱系統受制于其較低的散熱效率將逐漸難以滿足電池汽車未來的發展要求。為取長補短,充分發揮風冷散熱系統結構簡單、成本低的優點,可將風冷與其他一種或多種冷卻方式進行耦合應用,形成混合冷卻系統,達到提升整個散熱系統散熱能力的目的。
標簽:
汽車熱管理 點擊:
版權聲明:除非特別標注,否則均為本站原創文章,轉載時請以鏈接形式注明文章出處。