來源:洞見熱管理
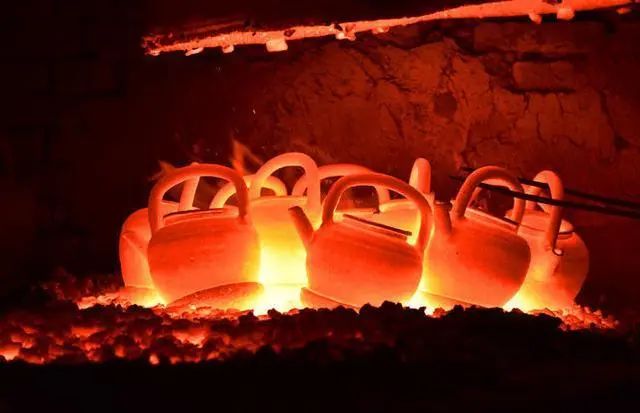
圖源:百度
01 燒結(jié)介紹
陶瓷燒結(jié)技術(shù)是人類在早期文明時(shí)期發(fā)展出的一種重要工藝,用于制作陶瓷器物。盡管古代技術(shù)水平有限,但古人已經(jīng)掌握了一些基本的燒結(jié)原理和方法。在古代,陶瓷制作是手工操作的,制作工藝主要包括制泥、成型、干燥和燒結(jié)等步驟。制泥時(shí),工匠會(huì)將粘土和其他原料混合攪拌,以形成陶泥。然后,陶工將陶泥塑成所需的形狀,如盤、碗、壺等。接著,制品會(huì)在陰干或晾曬后進(jìn)行燒結(jié)。古代的燒結(jié)設(shè)備主要是簡(jiǎn)易的土窯,將制品放入土窯中,用柴火燒制。
古代陶瓷燒結(jié)的溫度控制相對(duì)簡(jiǎn)單,通常是根據(jù)經(jīng)驗(yàn)和觀察進(jìn)行調(diào)節(jié)。陶瓷制品的燒結(jié)溫度通常在800°C到1200°C之間,這可以使粘土顆粒結(jié)合成堅(jiān)固的陶瓷體。總的來說,古代陶瓷燒結(jié)技術(shù)雖然簡(jiǎn)單,但為后世陶瓷工藝的發(fā)展奠定了基礎(chǔ),體現(xiàn)了人類對(duì)自然材料加工利用的智慧和創(chuàng)造力。
隨著時(shí)間的推移和技術(shù)的飛速發(fā)展和進(jìn)步,直到20世紀(jì)初期至中期:在這一時(shí)期,人們開始利用傳統(tǒng)的窯爐和燒結(jié)工藝,對(duì)陶瓷材料進(jìn)行燒結(jié)。這些技術(shù)主要基于傳統(tǒng)的加熱方法,如火爐、電爐等,雖然燒結(jié)效果已經(jīng)較為成熟,但存在能耗高、生產(chǎn)效率低等問題。20世紀(jì)后期:隨著科學(xué)技術(shù)的發(fā)展,微波加熱技術(shù)開始被應(yīng)用于陶瓷燒結(jié)領(lǐng)域。微波加熱具有加熱速率快、能耗低的優(yōu)勢(shì),因此被廣泛應(yīng)用于陶瓷材料的燒結(jié)工藝中。21世紀(jì)初期至今:隨著電子束、激光等新型加熱技術(shù)的應(yīng)用,陶瓷燒結(jié)技術(shù)得到了進(jìn)一步的發(fā)展。這些新技術(shù)具有加熱速率快、加熱均勻、能耗低等優(yōu)勢(shì),為陶瓷制造提供了更多可能性,尤其是在制備復(fù)雜結(jié)構(gòu)和高性能陶瓷制品方面有了重大突破。
02 燒結(jié)原理
陶瓷的燒結(jié)原理是指在高溫下,陶瓷粉末顆粒之間發(fā)生的結(jié)合過程,從而形成堅(jiān)固的陶瓷。從根本上說,燒結(jié)是粉末發(fā)生擴(kuò)散傳質(zhì)產(chǎn)生致密化,從而使陶瓷材料具有均勻顯微結(jié)構(gòu)、 穩(wěn)定形狀以及優(yōu)異性能的過程。在制備先進(jìn)陶瓷的過程 中,燒結(jié)是最重要的一個(gè)環(huán)節(jié)。在燒結(jié)過程中,降低燒結(jié)溫度、縮短燒結(jié)時(shí)間、細(xì)化晶粒、消除殘余氣孔是制 備高性能陶瓷材料的關(guān)鍵。
傳統(tǒng)上認(rèn)為陶瓷的燒結(jié)過程可以分為三個(gè)階段:
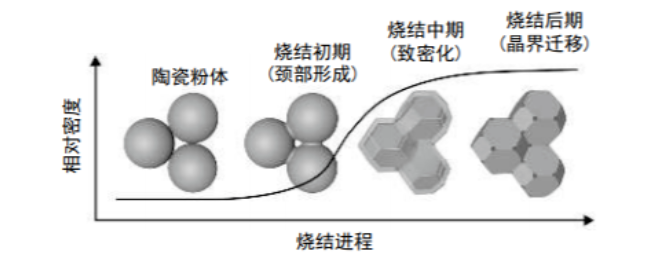
(1)燒結(jié)初期——粉體與顆粒之間相互接觸形成頸部燒結(jié)初期一般指顆粒和空隙形狀未發(fā)生明顯變化,線收縮率小于6%左右的階段。燒結(jié)物質(zhì)的接觸部分轉(zhuǎn)變成晶體結(jié)合并形成燒結(jié)頸部,通過表面擴(kuò)散和蒸發(fā)—凝聚發(fā)生物質(zhì)遷移而同時(shí)實(shí)現(xiàn)體積擴(kuò)散和晶界擴(kuò)散,從而使顆粒中心逐漸接近。由于表面擴(kuò)散和蒸發(fā)—凝聚過程僅是物質(zhì)的傳輸,物料中存在許多氣孔,晶界處于能量較低的狀態(tài),故晶粒不會(huì)長(zhǎng)大,所以燒結(jié)初期收縮比較小。但是燒結(jié)體的強(qiáng)度和其他性能等由于顆粒接觸面增大而有明顯的增加如果有液相存在,在此階段將會(huì)由于高溫時(shí)液相的產(chǎn)生而使顆粒重新分布而排列得更加致密,此時(shí)顆粒形狀和大小直接影響了顆粒間的堆積狀態(tài)和相互接觸情況,并最終影響燒結(jié)性能。(2)燒結(jié)中期——致密化速率增加,陶瓷快速收縮
進(jìn)入燒結(jié)中期頸部將進(jìn)一步增長(zhǎng),空隙進(jìn)一步變形和縮小顆粒之間的連貫氣孔通過晶界擴(kuò)散和體積擴(kuò)散排除,氣孔表面的物質(zhì)通過表面擴(kuò)散和蒸發(fā)—凝聚由曲率半徑小的表面向曲率半徑大的表面遷移,如圖所示形成單獨(dú)氣孔。在材料表面為開口氣孔,而內(nèi)部為孤立的封閉氣孔,同時(shí)形成晶界,開始了晶粒長(zhǎng)大過程,密度和強(qiáng)度顯著增加,一般在燒結(jié)中期材料的相對(duì)密度可以達(dá)到90%~95%。如果是相燒結(jié),那么在這個(gè)階段將是細(xì)小的顆粒和固體顆粒表面凸起部分在液相中溶解,并在粗顆粒表面上析出。(3)燒結(jié)后期——致密化速率急速下降,晶界遷移并導(dǎo)致陶瓷晶粒長(zhǎng)大
燒結(jié)后期多數(shù)空隙已成為孤立的閉氣孔,存在于晶界的氣孔通過氣孔的表面張力和晶界張力趨于平衡,封閉氣孔收縮成類似球形并且氣孔數(shù)大為減少。而物質(zhì)通過體積擴(kuò)散使得內(nèi)部晶粒開始緩慢地均勻長(zhǎng)大,并推動(dòng)氣孔移動(dòng)促使氣孔沿晶界通道排除達(dá)到致密化,但仍然殘留少量的封閉氣孔。不管是哪一個(gè)階段的燒結(jié),都會(huì)引起宏觀尺寸的收縮和致密度增加,因此通常用收縮率或密度值來度量燒結(jié)的程度。燒結(jié)過程中推導(dǎo)物質(zhì)傳遞和遷移從而實(shí)現(xiàn)致密化過程的動(dòng)力主要由顆粒的表面能提供。而系統(tǒng)表面能的大小由表面張力和顆粒大小、凹凸等因素決定。燒結(jié)過程中的物質(zhì)遷移導(dǎo)致致密化作用和晶粒成長(zhǎng)。溫度提高時(shí)物質(zhì)的遷移率增加,則晶粒更容易成長(zhǎng)。晶粒的形成首先由顆粒的接觸長(zhǎng)大開始,當(dāng)頸部區(qū)形成晶界且寬度長(zhǎng)大到相當(dāng)于小顆粒的尺寸時(shí),晶界將較為迅速地掃過小顆粒,兩個(gè)顆粒便形成一個(gè)晶粒。而理想的微觀結(jié)構(gòu)是盡可能控制晶粒小而均勻,排除構(gòu)成缺陷的氣孔而接近于理論密度,沒有殘存的殘留應(yīng)力,因此,陶瓷材料的低溫?zé)Y(jié)日益引起人們的重視。另外,晶粒生長(zhǎng)也和晶粒的大小有關(guān),平均粒徑小的粒子發(fā)生收縮后越發(fā)變小,而大的粒子將其合并越發(fā)變大,在大粒子周圍彎曲的晶界兩側(cè)存在著自由能之差 AG,因此,晶界向曲率中心遷移,粒子成長(zhǎng)。
03 燒結(jié)技術(shù)分類
隨著材料科學(xué)和工程技術(shù)的不斷發(fā)展,陶瓷燒結(jié)技術(shù)也在不斷創(chuàng)新和改進(jìn),為陶瓷制造領(lǐng)域的發(fā)展提供了更多可能性。其中傳統(tǒng)的燒結(jié)是在外加熱場(chǎng)與常壓或機(jī)械壓力的作用下完成的,但是這些方法對(duì)特定材料體系的燒結(jié)具有局限性。所謂傳統(tǒng)燒結(jié)技術(shù)就是陶瓷粉末被加熱至其熔點(diǎn)以下的溫度,使其顆粒間的結(jié)合力增強(qiáng),形成致密的塊狀物體。這種技術(shù)存在能耗高、燒結(jié)時(shí)間長(zhǎng)和產(chǎn)品易變形等問題。近年來,國(guó)內(nèi)外學(xué)者開發(fā)了多種能夠顯著改善陶瓷材料燒結(jié)狀況的新工藝,例如微波燒結(jié)、放電等離子燒結(jié) 、閃燒 、冷燒結(jié)、振蕩壓力燒結(jié)等;這些燒結(jié)新技術(shù)的產(chǎn)生為高性能陶瓷材料的制備開辟了新方法,并且豐富了陶瓷材料的燒結(jié)理論。微波燒結(jié)技術(shù):微波燒結(jié)原理與傳統(tǒng)燒結(jié)有著本質(zhì)區(qū)別。微波燒結(jié)技術(shù)利用微波加熱原理,將陶瓷粉末迅速加熱至高溫,加快了燒結(jié)速率,縮短了燒結(jié)周期,并且能耗相對(duì)較低;一般的微波燒結(jié)裝置主要由微波源系統(tǒng),微波傳輸系統(tǒng),微波燒結(jié)腔和監(jiān)測(cè)控制系統(tǒng)4部分組成。其結(jié)構(gòu)如圖所示。
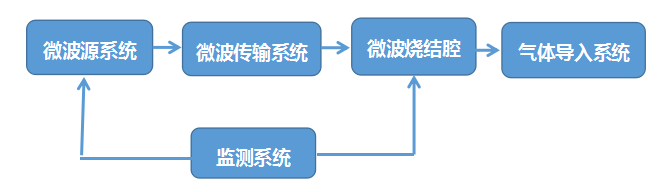
圖2:微波燒結(jié)結(jié)構(gòu)裝置示意圖
放電等離子燒結(jié):利用放電等離子體在高溫下對(duì)陶瓷粉末進(jìn)行加熱和燒結(jié)的過程;該技術(shù)開創(chuàng)性地將直流脈沖電流引入燒結(jié)過程,壓頭在向材料 施加壓力的同時(shí)也充當(dāng)電流通過的載體。與傳統(tǒng)燒結(jié)技術(shù)通常利用發(fā)熱體輻射加熱不同,SPS 技術(shù)借助大電流 通過模具或?qū)щ姌悠樊a(chǎn)生的熱效應(yīng)來加熱材料。對(duì)于絕緣樣品,通常使用導(dǎo)電性良好的石墨作為模具材料,利用模具的電阻熱使樣品快速升溫; 對(duì)于導(dǎo)電樣品,則可 以使用絕緣模具,使電流直接通過樣品進(jìn)行加熱。其升溫速率可達(dá) 1000 ℃ /min,當(dāng)樣品溫度達(dá)到設(shè)定值后,經(jīng)過短時(shí)間保溫即可完成燒結(jié)。
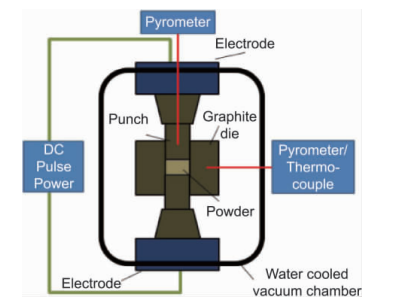
圖3:SPS 設(shè)備的工作原理示意圖
閃燒結(jié)技術(shù):閃燒結(jié)技術(shù)是一種高溫快速燒結(jié)技術(shù),通過在極短時(shí)間內(nèi)將陶瓷粉末加熱至高溫,使其在幾秒鐘內(nèi)完成燒結(jié)過程,具有燒結(jié)速率快、能耗低的優(yōu)勢(shì);FS 技術(shù)于 2010 年由科羅拉多大學(xué)的 Cologna 等首次報(bào)道,其來源于對(duì)電場(chǎng)輔助燒結(jié)技術(shù)( field-assisted sintering technology,F(xiàn)AST) 的研究。圖4是一種典型的 FS 裝置示意圖,待燒結(jié)陶瓷素坯被制成“骨頭狀”,兩端通 過鉑絲懸掛在經(jīng)過改造的爐體內(nèi),向材料施加一定的直 流或交流電場(chǎng)。爐體內(nèi)有熱電偶用于測(cè)溫,底部有 CCD 相機(jī)可實(shí)時(shí)記錄樣品尺寸。
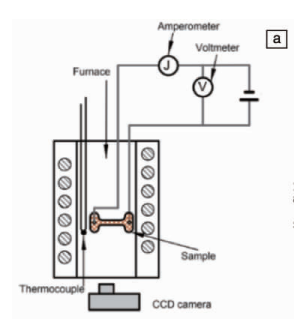
冷燒結(jié):冷燒結(jié)利用化學(xué)反應(yīng)或者機(jī)械壓縮等方法,將陶瓷粉末顆粒結(jié)合在一起,形成堅(jiān)固的陶瓷體;圖4為冷燒結(jié)技術(shù)的工藝流程圖,陶瓷 CS 技術(shù)的基本工藝是在陶瓷粉體中加入少量水溶液潤(rùn)濕顆粒,粉體表 面物質(zhì)分解并部分溶解在溶液中,從而在顆粒-顆粒界面 間產(chǎn)生液相。將潤(rùn)濕好的粉體放入模具中,并對(duì)模具進(jìn)行加熱,同時(shí)施加較大的壓力,保壓保溫一段時(shí)間后可制備出致密的陶瓷材料。

圖5:冷燒結(jié)技術(shù)的設(shè)備振蕩壓力燒結(jié):現(xiàn)有的各種壓力燒結(jié)技術(shù)采用的都是靜態(tài)的恒定壓力,燒結(jié)過程中靜態(tài)壓力的引入,雖有助于氣孔排除和陶瓷致密度提升,但難以完全將離子鍵和共價(jià)鍵的特種 陶瓷材料內(nèi)部氣孔排除,對(duì)于所希望制備的超高強(qiáng)度、 高韌性、高硬度和高可靠性的材料仍然具有一定的局限性。振蕩壓力燒結(jié)將振蕩和壓力結(jié)合起來,通過施加振蕩力和壓力使陶瓷粉末在高溫下形成致密的陶瓷制品。
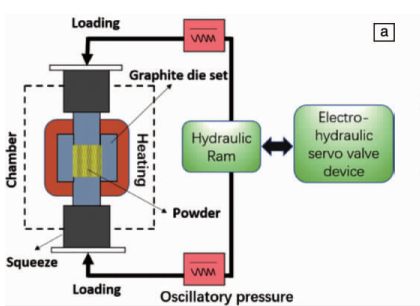
圖6:振蕩壓力燒結(jié)設(shè)備示意圖
04 燒結(jié)論
先進(jìn)功能陶瓷材料以其一系列優(yōu)異的性能,在工業(yè)領(lǐng)域 扮演著至關(guān)重要的角色,然而目前陶瓷材料的廣泛應(yīng)用 仍面臨許多問題與挑戰(zhàn),其中可靠性、致密度和強(qiáng)度是 主要的制約因素。如何在較低燒結(jié)溫度下實(shí)現(xiàn)材料的快速致密化,制備出完全無氣孔、結(jié)構(gòu)均勻、晶粒細(xì)小且晶界強(qiáng)化的陶瓷塊體仍是陶瓷材料科學(xué)工作者不斷追求 的目標(biāo)。長(zhǎng)期以來,研究人員分別從納米陶瓷粉體的制備與性能調(diào)控、陶瓷燒結(jié)工藝與燒結(jié)基礎(chǔ)理論、燒結(jié)新技術(shù)與新裝備等領(lǐng)域進(jìn)行了廣泛而深入的研究。結(jié)果顯 示,制造技術(shù)與制造設(shè)備的革命,尤其是陶瓷燒結(jié)設(shè)備與燒結(jié)技術(shù)的創(chuàng)新是進(jìn)一步提高先進(jìn)陶瓷材料性能的最關(guān)鍵因素。未來需要學(xué)術(shù)界和產(chǎn)業(yè)界密切合作共同協(xié)作努力進(jìn)一步挖掘新燒結(jié)技術(shù)的應(yīng)用潛力。
標(biāo)簽:
導(dǎo)熱界面材料 點(diǎn)擊:
版權(quán)聲明:除非特別標(biāo)注,否則均為本站原創(chuàng)文章,轉(zhuǎn)載時(shí)請(qǐng)以鏈接形式注明文章出處。