摘要:底部填充膠(Underfill)作為一種重要的集成電路封裝電子膠粘劑,在先進封裝如 2.5D、3D 封裝中,用于緩解芯片封裝中不同材料之間熱膨脹系數不匹配帶來的應力集中問題,進而提高器件封裝可靠性。在各種底部填充材料中,環氧樹脂基底部填充膠是最常用的,也是商業化最成熟的產品。然而,廣泛使用的毛細管環氧基底部填充膠材料的導熱系數較低,無法滿足功率密度更高的下一代先進封裝芯片不斷增長的散熱要求。盡管已經發明了許多提高環氧樹脂導熱系數的策略,但其作為性能要求復雜的底部填充材料的應用仍然很困難,優化用于倒裝芯片封裝用底部填充材料的熱-電-機械性能仍然是一個巨大的挑戰。本文回顧了導熱環氧樹脂基底部填充膠材料為滿足關鍵散熱要求而取得的最新進展。同時,為高功率密度電子器件的電子封裝設計具有高導熱高可靠性的底部填充材料提供思路。電子封裝,從20世紀50年代的通孔技術(THT)、80 年代的表面貼裝技術(SMT)、90 年代的球柵陣列(BGA)和 21世紀初的芯片級封裝(CSP)迅速發展起來。因為倒裝芯片提供更高的輸入/輸出(I/O)密度、更短的互連、更好的散熱、小尺寸和低輪廓,使得芯片的有源面朝下,并通過焊點直接與基板互連的倒裝芯片技術,已經成為 CSP 最具吸引力的一種封裝方法。盡管倒裝芯片封裝比傳統的引線鍵合有許多優點,但仍存在諸如散熱難的問題和挑戰。由于 IC 芯片(硅CTE,約 2.5 ppm/K)和基板(FR-4 CTE,18~24 ppm/K)之間的熱膨脹系數(CTE)不匹配,會對焊點(CTE 22~26 ppm/K)施加大的熱機械應力,導致熱循環過程中失效。1987年,日立公司展示了一種新方法,通過在芯片與基底之間填充具有良好附著力的可固化樹脂,有效地重新分配了熱應力。1996 年,WONG 等首先提出了無流動填充技術,大大提高了底部填充工藝的生產效率。在隨后的幾年里,模壓填充、晶圓級填充和其他底部填充工藝也被開發出來,以滿足倒裝芯片封裝日益增長的功能要求。試驗證明,底部填充膠可以降低關鍵焊點 10%~25% 的應力緩沖能力,極大地提高了器件的可靠性。此外,底部填充膠可以保護芯片和焊點免受氧氣和水分的腐蝕,以及機械應變,如沖擊、跌落和振動,進一步提高電子元器件的可靠性。根據倒裝封裝填充工藝,目前的填充工藝主要分為毛細管底部填充、無流動底部填充和模壓底部填充工藝。由于毛細管底部填充工藝簡單、形成不完全填充和空隙缺陷的概率較低,兼容性更好,在實際應用中得到廣泛應用,并覆蓋了超過 60%的底部填充市場。毛細管底部填充工藝是在基板上加入助熔劑,將芯片有源面倒置在基板上,通過回流焊將芯片與基板相連,清理剩余助熔劑。組裝后,底部填充膠利用毛細現象施膠填入芯片與基板的空隙中。最后通過加熱固化,完成封裝,具體過程如圖1所示。

一般而言,底部填充膠應具有低黏度,以便其能夠容易地流動并完全填充芯片和基板之間的間隙。與焊點之間的CET 較小,以及較高的玻璃化轉變溫度(Tg),以確保電子設備即使在較高工作溫度下的可靠性。底部填充膠的彈性模量和斷裂性能也與器件的完整性和可靠性有關。此外,底部填充膠應采用電絕緣材料(避免短路)、介電常數低(保證信號傳播速度高)、介電損耗系數低(減少信號損耗)。半導體集成電路技術在過去的 50 年里發展迅速,晶體管柵極長度已經從 10 μm 減少到 4 nm,并且芯片堆疊技術已經實現了從 2D、2.5D 演變到 3D,并伴隨著局部功率密度達到100 W/cm2以上。集成電路芯片在積累熱量時產生的過量熱量會導致溫度的急劇上升,從而呈指數級降低電子設備的壽命。因此,高效的散熱也是保證其可靠性和性能的關鍵。用于電子封裝的理想高性能底部填充材料應同時具有高導熱系數(>1.0 W·m–1·K–1)、高電阻率(>1012 Ω·cm)、低黏度(298 K 時<20 Pa·s)、適當的 CTE(25~30 ppm/K)、高 Tg(>398 K)、低介電常數(298 K 和 1 kHz 時 <4.0)和低的介電損耗因子(298 K和1 kHz時<0.005),如表1所示。
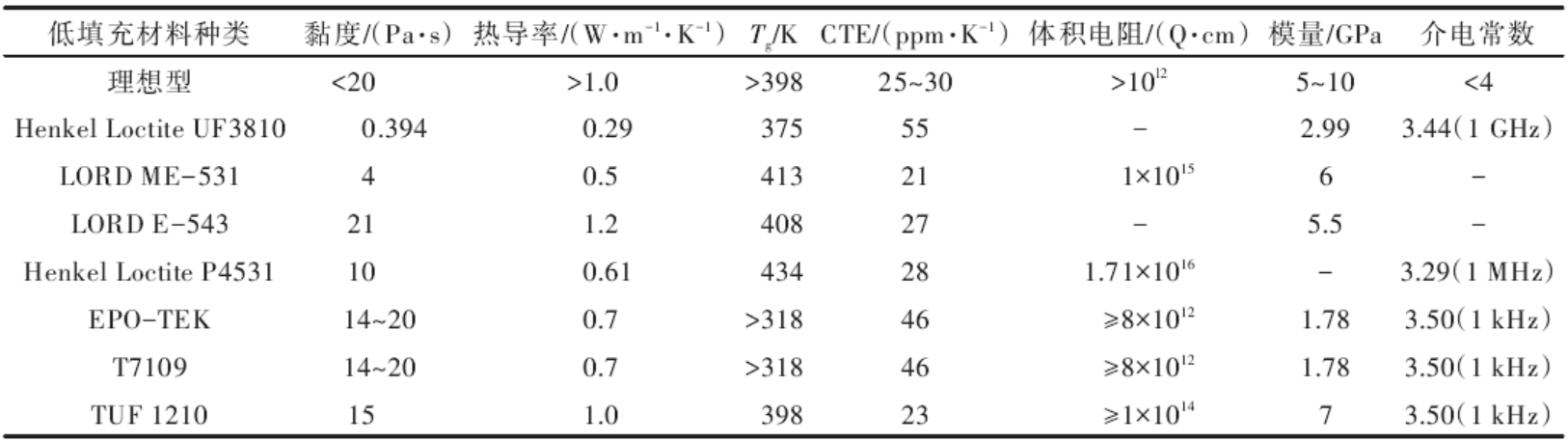
然而,傳統的環氧基底填充材料的導熱系數通常低于 0.4 W/(m·K),這很難滿足不斷增加的散熱要求。SEO 等通過試驗證明,隨著底填充材料的導熱系數從 0.4 W/(m·K)增加至 1.0 W/(m·K),封裝的熱阻降低了 22%,導致更好的散熱。因此,底填充材料的導熱系數對于功率密度不斷增加的微電子技術非常重要。通常,為提高導熱性能,通過在環氧樹脂中加入大量的導熱無機填料,可以提高底填材料的導熱性。但無機填料的存在增加了底部填充膠的黏度,填充時間更長,難以消除流動過程中內部的空隙,導致應力集中而失效。因此,制造具有組合熱-電-機械性能,特別是高導熱系數和低黏度的底填材料是迫切的需要和挑戰。環氧樹脂具有良好的力學性能、高耐熱性和易加工性,因此被廣泛用于倒裝芯片底部填充材料。但固化的環氧基團內部無序的非晶態鏈結構導致嚴重的聲子散射和低的傳熱效率,因此傳統的環氧樹脂導熱系數一般在 0.2 W/(m·K)以下,限制了其作為底部填充材料的散熱能力。將高導熱性填料加入到環氧樹脂中已被證明是一種簡便、有效的方法,可以提高導熱性,同時保持良好的加工性/流動性。這是制造倒裝芯片底部填充材料最常用且最有前景的一種策略。WEI 等采用溶膠-凝膠法合成了富含 SiO2涂層的多壁碳納米管(MWCNT@SiO2),并將其加入環氧基體中,如圖2所示。
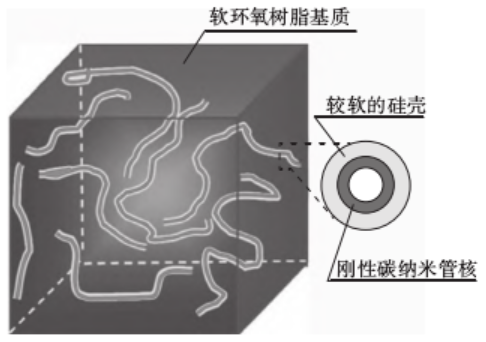
圖2 MWCNT@SiO2及其環氧樹脂復合材料的示意圖較弱的硅中間殼不僅緩解了多壁碳納米管與軟環氧樹脂之間的模量不匹配,而且改善了它們之間的相互作用。環氧樹脂/MWCNT@SiO2復合材料的熱導率在低負載量為 0.5% 和 1% 時,分別提高了51% 和 67%。同時,硅殼層保持了環氧復合材料的高電阻率,如圖3所示。

這種 SiO2涂層策略已廣泛應用于高固有導熱性填料,可用于實現高導熱性和電絕緣的環氧復合材料。HSIAO 等報道了由熱還原氧化石墨烯(TRGO)和 SiO2組成的夾層結構的混合納米片,如圖 4所示。
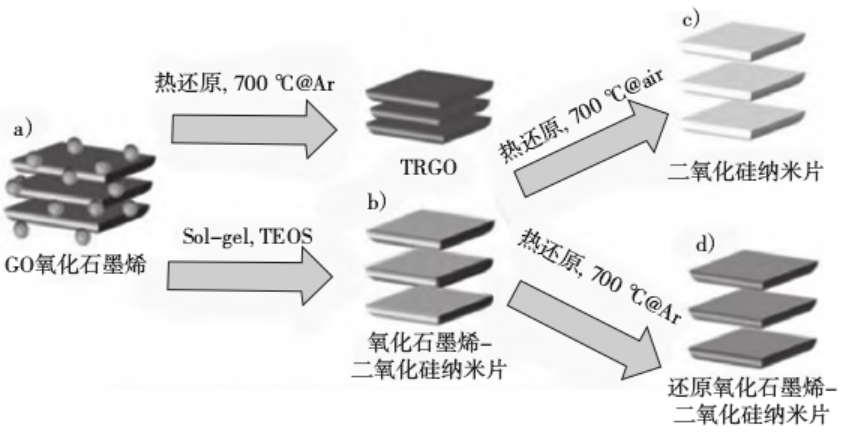
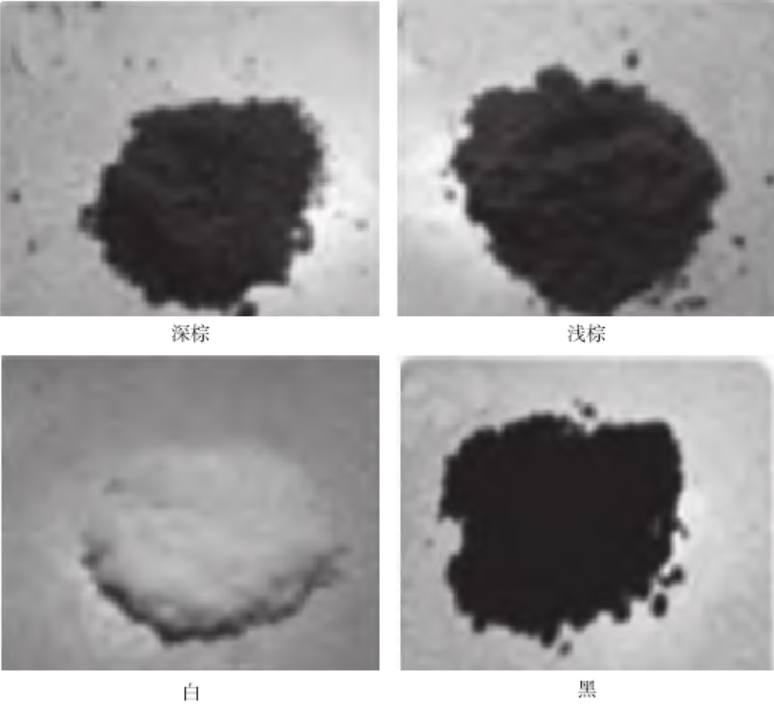
圖4 氧化石墨烯(GO)-SiO2、SiO2和熱還原氧化石墨烯(TRGO)-SiO2納米片的制備流程圖
SiO2層覆蓋了 TRGO 的表面,阻礙了導電并有效地形成了3D聲子傳輸通道,該通道對環氧樹脂基體的電學和熱學性能具有獨特的影響。單純的環氧樹脂的熱導率為 0.2 W/(m·K),而含有 1%TRGO-SiO2環氧納米復合材料的熱導率為 0.322 W/(m·K),提高了61%。JIANG 等通過在不同長度/直徑比值的AgNWs 表面包覆二氧化鈦(TiO2)涂層(命名為AgNWs@TiO2),并評估了對環氧樹脂/銀納米線(epoxy/AgNWs)復合材料的彈性模量失配對熱導率的影響,結果如圖 5 和圖 6 所示。

圖5 AgNWs@TiO2、epoxy/AgNWs@TiO2的微觀形貌與 epoxy/AgNWs復合材料相比,AgNWs@TiO2可以更均勻地分散在環氧樹脂基體中,具有較高彈性模量的 TiO2層增加了與環氧樹脂的模量失配,加劇了界面聲子散射,在填料體積分數 4.0% 的時,epoxy/AgNWs@TiO2復合材料的熱導率為 0.673 W/(m·K)。此外,epoxy/AgNWs@TiO2復合材料相對于環氧樹脂/AgNWs 復合材料具有更高的體積電阻率和更低的介電性能。石墨烯由于其優異的寬高比和導熱性可以顯著提高聚合物的導熱性,但石墨烯會導致電絕緣性嚴重降低,從而限制了其聚合物復合材料在電子和系統熱管理中的廣泛應用。為了解決這個問題,北京化工大學于中振教授團隊使用電絕緣的Al2O3來裝飾高質量(無缺陷)石墨烯納米片(GNP)。在超臨界二氧化碳(scCO2)的輔助下,通過高溫煅燒制備了 Al2O3@GNP 復合材料,具有 12%Al2O3@GNP 雜化物的環氧樹脂復合材料具有 1.49 W/(m·K)的高熱導率,比純環氧樹脂高 677%,表明其作為環氧基導熱型底部填充膠材料的巨大潛力,如圖 7 和圖 8所示。

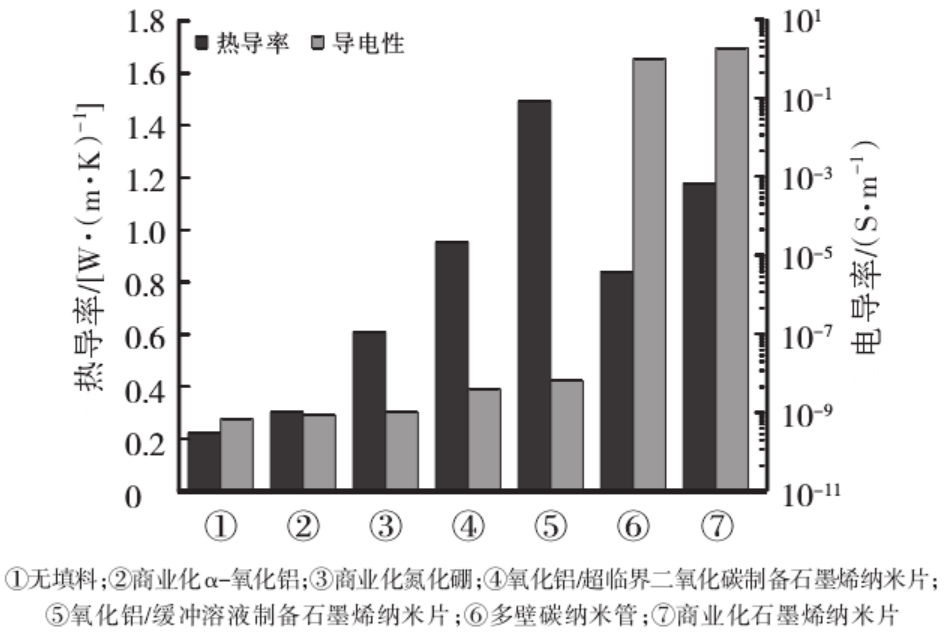
MAO 等報道了由核殼結構 Al@Al2O3和環氧樹脂組成的導熱絕緣熱界面材料。在填料含量為 60%時,復合材料的導熱系數為 0.92 W/(m·K),比環氧樹脂的導熱系數高約 4.2 倍。DU 等通過將氧化鎂涂層的石墨烯(MgO@GR)納米材料摻入環氧樹脂基體中,環氧樹脂的性能得到改善。添加MgO 涂層不僅改善了石墨烯在基體中的分散性和石墨烯與環氧樹脂之間的界面結合,而且提高了環氧樹脂的導熱性。添加 7% MgO@GR 后,環氧樹脂納米復合材料的熱導率比純環氧樹脂提高了76%。除了 SiO2、TiO2、Al2O3以及 MgO 等無機填料以外,其他具有較高導熱性能的填料也經常被用于底部填充膠材料,如氮化硼(BN,60 W·m–1·K–1)等。一般而言,填充有納米結構核殼導熱填料的環氧樹脂復合材料的熱導率高于嵌入未經處理的導電填料的環氧樹脂復合材料。絕緣材料中熱傳導的主要載體是聲子,它是由晶格振動(在晶體材料中)或原子振動(在非晶材料中)產生的。在聲子傳播過程中,任何晶格不連續都會導致聲子散射并產生界面電阻。一般來說,高導熱材料的高頻聲子模式在被傳輸到相鄰材料之前,會通過聲子-聲子耦合轉移或分裂成低頻聲子模式。密度和固有聲速(聲子頻率)差異較大的兩種材料將提供更大的聲阻抗和界面熱阻。因此,兩種材料之間的聲子頻率失配越高,通過界面傳輸的聲子就越少,從而導致傳熱效率降低。不同材料之間的聲子頻率失配程度是很難快速估計的。然而,德拜溫度(Debye Temperature)是激活最大聲子頻率并描述原子振動特性的溫度。因此,Debye 溫度通常用于定性分析不同材料之間的界面熱阻(Rk)。此外,Debye 溫度與材料中的平均聲子速率成正比并反映其彈性剛度,高彈性剛度表明晶格內的原子間相互作用有利于聲子傳輸。因此,具有高彈性模量的材料,如碳納米管、石墨烯和金剛石,具有高 Debye 溫度和高晶格熱導率。相比之下,聚合物通常具有較弱的彈性模量,表明平均聲子速率較慢且熱導率較低。在剛性填料和低剛性聚合物之間加入中間彈性模量層,可以降低界面材料的聲子頻率差,從而降低界面熱阻并提高其復合材料的導熱率。CHAO 等通過靈活的溶膠-凝膠法合成了二氧化硅涂層的銀納米線(AgNWs@SiO2),然后摻入環氧樹脂中。SiO2的楊氏模量為 70 GPa,環氧樹脂基體和 AgNWs 分別為 3 GPa 和 102 GPa。因此,AgNWs 上硬度較低的二氧化硅中間納米層不僅減輕了 AgNWs和環氧樹脂之間的模量不匹配,而且增強了它們的界面相互作用。填充量為 4 vol.%的環氧樹脂/AgNWs@SiO2復合材料的熱導率從純環氧樹脂的 0.19 W/(m·K)增加到 1.03 W/(m·K),而具有相同納米線的環氧樹脂/AgNWs 復合材料的熱導率為0.57 W/(m·K)。因此,二氧化硅納米層就像一個跳板,可以降低聲子傳播勢壘,降低界面熱阻并提高環氧樹脂/AgNWs 納米復合材料的導熱性。同時,絕緣 SiO2納米層有效地避免了在環氧樹脂中形成AgNWs 的導電網絡,從而使復合材料具有高電絕緣性。具有核殼結構的 AgNWs@SiO2納米線也改善了環氧樹脂的介電性能。因此,這些環氧樹脂/AgNWs@SiO2復合材料具有適合電子封裝底部填充材料的潛力,如圖9和圖10所示。
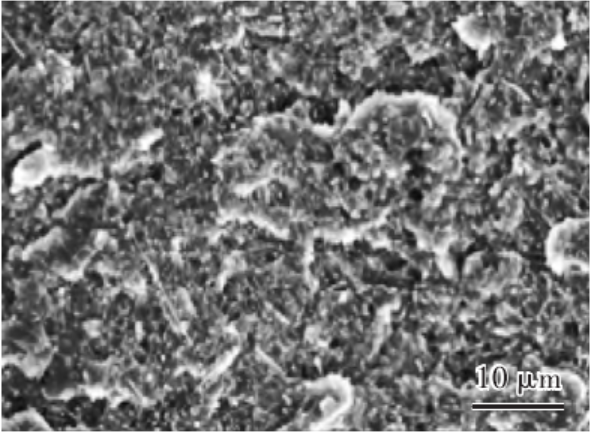
圖9 環氧樹脂/AgNWs@SiO2復合材料的SEM
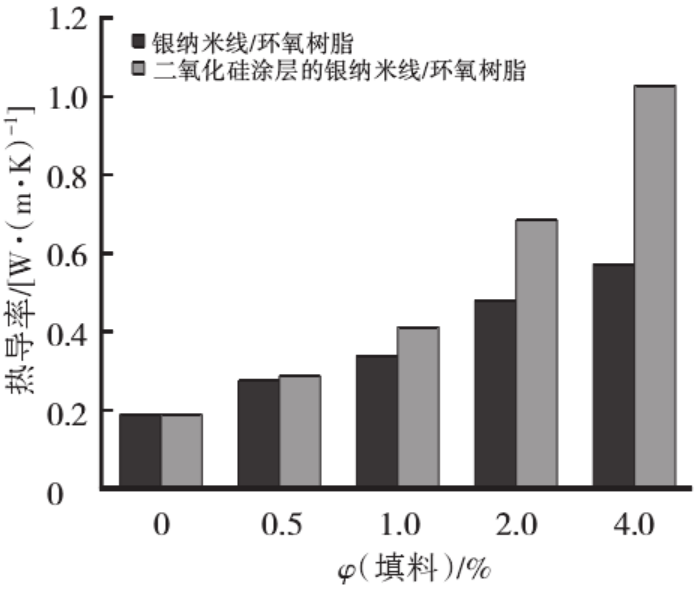
圖10 環氧樹脂/AgNWs和環氧樹脂/AgNWs@SiO2材料的導熱性能不僅可以通過在填料上引入中間模量層來降低環氧樹脂基體和填料之間的整體界面熱阻,還可以通過在填料表面添加官能團來降低界面熱阻。LOSEGO 等在試驗中發現,界面相互作用強度直接決定了兩種材料界面上的聲子熱傳輸過程。隨著界面相互作用從范德華力轉變為共價鍵,石英基板和金膜界面之間的界面熱導率增加了 80%。WANG 等使用分子動力學模擬,研究了官能團對功能化石墨烯和環氧樹脂之間的聲子轉移影響。與原始石墨烯相比,功能化石墨烯的聲子振動功率譜與環氧樹脂基質的重疊顯著增加,表明功能化石墨烯和環氧樹脂之間的聲子耦合要好得多。由于官能團增強了石墨烯和環氧樹脂之間的相互作用,它們的基體-填料界面熱導率增加,從而提高了復合材料的熱導率,如圖11所示。
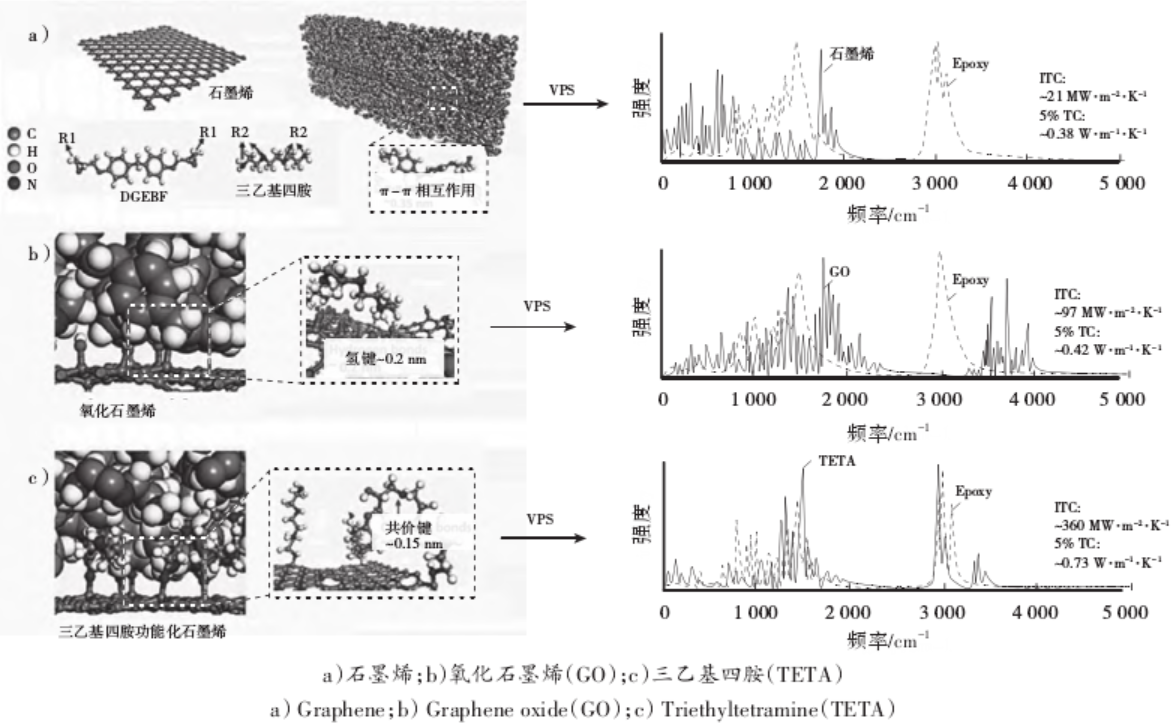
圖11 石墨烯、氧化石墨烯(GO)和三乙基四胺(TETA)功能化石墨烯為填料的環氧樹脂復合材料的分子模型和聲子振動功率譜通過表面改性降低界面熱阻已被廣泛用于通過減少界面處的聲子散射,來提高填料負載復合材料的導熱性。JIANG 等通過自由基聚合接枝聚甲基丙烯酸縮水甘油酯(PGMA)于 BN 表面。用PGMA 對 BN進行表面改性增強了 BN和環氧樹脂之間的界面相互作用,從而降低了界面電阻。因此,具有體積分數 15% 的 PGMA 接枝 BN 的環氧復合材料顯示出 1.2 W/(m·K)的熱導率,比填充原始 BN 的高約15%。良好的填料分散有助于通過增強填料與填料的連通性形成導熱路徑。YAN 等開發了一種簡便、省時且可擴展的方法,通過在環氧樹脂基體中原位球磨 BN 來制造導熱但低黏度的環氧樹脂復合材料,如圖12所示。
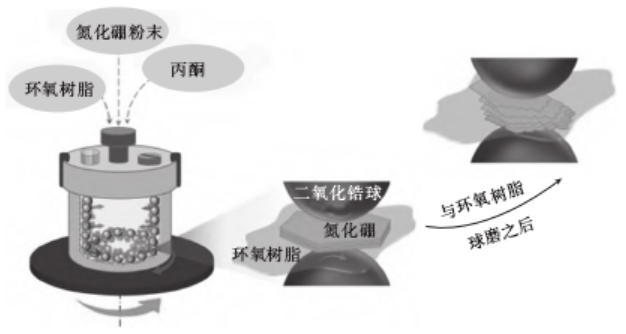
環氧樹脂輔助研磨大大改善了 BN 片晶在基體中的分散性,含有 9.1% 球磨 BN 的環氧樹脂復合材料顯示出 0.44 W/(m·K)的熱導率,比沒有球磨制備的復合材料熱導率提高了37%。與單一填料相比,混合填料可以通過增加填料填充密度和互連性來建立有效的導熱路徑,從而進一步提高復合材料的導熱性。HAN 等通過超聲波浸漬、溶膠-凝膠和碳熱還原等方法構建了一種巢狀異質結構 BNNS@SiCnws導熱填料。然后,采用共混澆注法制備了導熱絕緣 BNNS@SiCnws/環氧樹脂復合材料。當BNNS@SiCnws-II(質量比為65/35)作為填料的用量為 20% 時,BNNS@SiCnws/環氧樹脂復合材料的整體性能最佳。導熱系數從純環氧樹脂基體的 0.22 W/(m·K)增加到 1.17 W/(m·K),高于SiCnws/環氧樹脂(0.72 W·m–1·K–1)和 BNNS/環氧樹脂(0.82 W·m–1·K–1)。同時,BNNS@SiCnws/環氧樹脂復合材料表現出優異的傳熱/散熱效率。這是由于SiCnws和BNNS“線對面”異質結構的協同作用,可以顯著提高導熱路徑的形成概率,如圖 13 和圖 14所示。
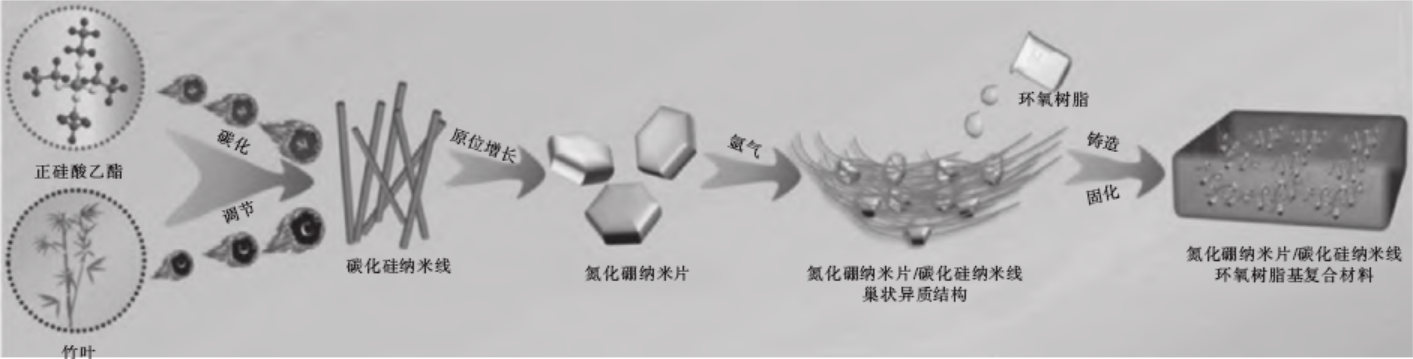
圖13 巢狀異質結構BNNS@SiCnws導熱填料及其導熱和電絕緣BNNS@SiCnws/環氧復合材料的制造示意圖
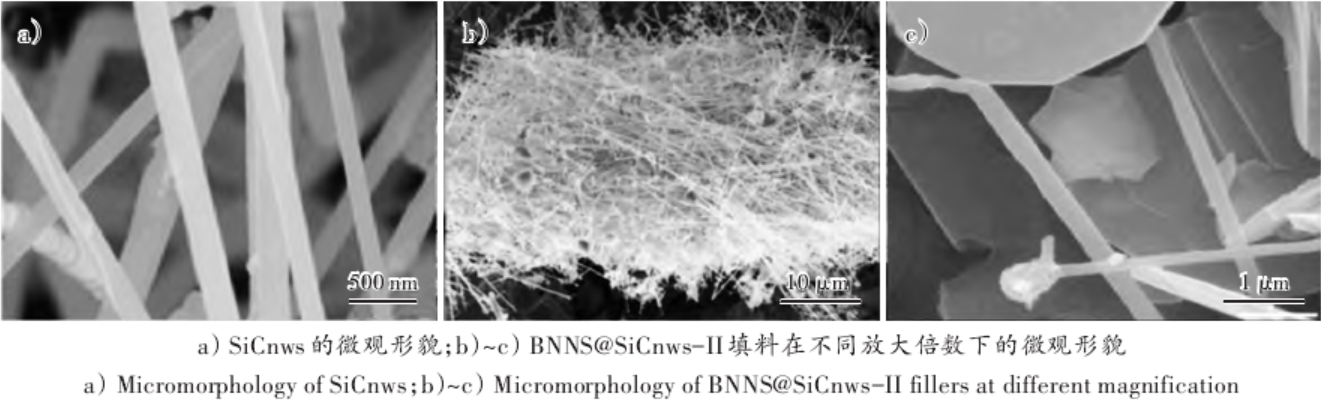
圖14 SiCnws和BNNS@SiCnws-II填料的微觀形貌通過燒結金屬或共價鍵橋接相鄰的填料,形成有效的熱傳輸結來降低接觸熱阻,從而提高復合材料的熱導率。華中科技大學解孝林教授等通過在氮化硼納米片(BNNS)表面原位燒結銀納米顆粒,在環氧樹脂復合材料中形成具有良好填料-填料界面接觸的連續導熱網絡。在這種復合材料中,均勻分散且剝離良好的 BN 納米片通過位于 BNNS 處的燒結 AgNPs 相互橋接,并形成 3D 氮化硼納米片網絡。熱燒結后,環氧樹脂/BNNS@AgNPs 復合材料與3D 氮化硼納米片網絡的熱導率在 20% 的填充量下從 0.95 W/(m·K)增加到 1.13 W/(m·K)。這表明合并 AgNPs 用作熱傳輸結,可以降低 3D BNNS 網絡中的熱接觸電阻,如圖15所示。
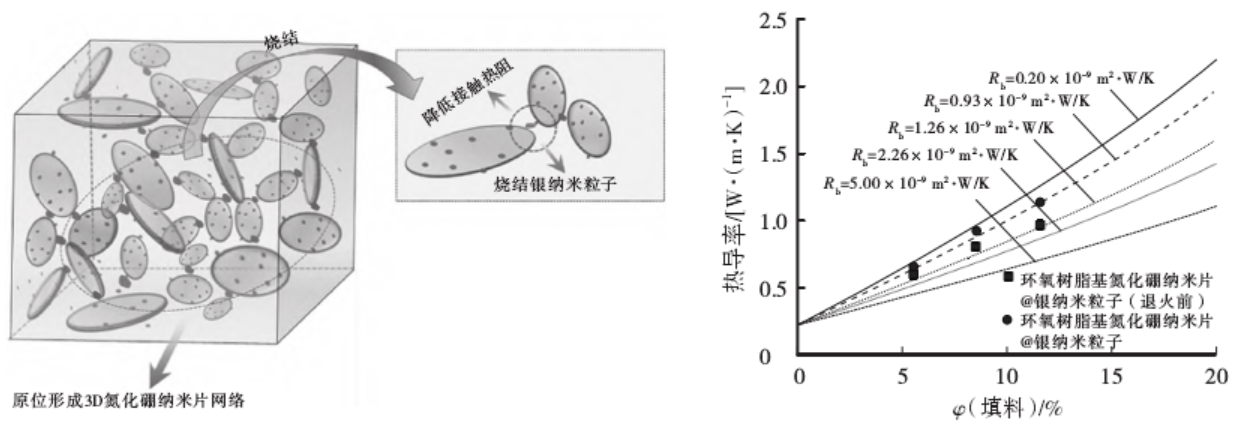
圖15 環氧樹脂/BNNS@AgNPs復合材料降低接觸熱阻除了上述提到的增強環氧基復合材料的導熱性能以外,還可以將導熱填料選擇性地定位在一個聚合物相中或兩種不混溶的聚合物共混物的界面,或在導熱多孔填料骨架中滲透環氧樹脂等,均已被證明能有效地增強環氧復合材料的導熱系數。然而,由于其他難以滿足的嚴格要求,這些方法難以應用于底部填充工藝。(1)綜述了環氧樹脂基復合材料作為導熱底部填充膠材料的研究進展,研究表明添加 SiO2、TiO2、Al2O3、MgO、BN、SiC以及Ag等無機填料或CNT、石墨烯等碳材料可以提高環氧基復合材料的導熱性能。(2)通過構建界面模量層、界面填料的表面修飾、提高填料的分散性、構建混合填料網絡結構、降低接觸熱阻等方式,可以大大提高環氧基復合材料的導熱性能。(3)具有高固有導熱性能的 Ag、SiC、CNT 和石墨烯等填料比目前商業化的 SiO2填料的價格更高,限制了其產業化應用。未來需要通過學術界和工業界的共同努力,以低成本規模化生產更高導熱型環氧樹脂基底部填充膠材料。(4)精確設計特定的環氧樹脂分子結構(比如具有特定官能團的環氧樹脂、修飾烷氧基硅基基團、阻燃基團和環氧玻璃體等大分子)可以提高環氧樹脂本征導熱性能、降低黏度、增強尺寸穩定性、提高阻燃性等特性,為先進封裝,如 2.5D、3D等封裝結構設計性能更加優異的底部填充膠材料。
標簽:
導熱散熱 點擊:
版權聲明:除非特別標注,否則均為本站原創文章,轉載時請以鏈接形式注明文章出處。