摘要:隨著電子產品向小型化、多功能、大功率發展以及集成度的不斷提高,必然會帶來熱量更為集中、熱流密度不斷升高的問題。為保證可靠工作,實現電子產品,尤其是高密度集成微系統的高效散熱就顯得尤為重要。與傳統的散熱技術相比,微通道散熱器可直接集成在器件/系統基板內,制造工藝兼容性好,散熱路徑短、散熱能力強,特別適用于高密度集成微系統的熱管控。本文綜述了微通道散熱器傳熱傳質特性的表征、影響因素及強化方法。對微通道結構進行優化設計、采用以納米流體為代表的高性能冷卻介質是提高微通道散熱器綜合散熱性能的主要手段。目前在復雜三維微通道結構的制造及高穩定納米流體性能調控等方面還存在諸多問題。深入研究相關制造工藝技術和傳熱傳質機理,將有利于進一步拓展微通道散熱技術在高密度集成微系統熱管控領域的實際應用。
高密度集成封裝是電子器件和微系統性能提高、尺寸減小并實現多功能化等的重要途徑。然而,集成度越來越高的同時,器件和微系統的散熱面積變小、熱流密度越來越高、熱量更加集中的問題也隨之變得突出。例如刀片式服務器 CPU 的峰值熱流密度為80~200 W/cm2,大功率激光器和微波器件工作時的熱流密度可達 1000 W/cm2。電子產品的熱流密度過大,將導致溫度的急劇上升。研究發現,電子元器件的可靠性對溫度十分敏感。當電子元器件的工作溫度達到 70~80℃ 后,溫度每上升 1℃,其可靠性就會降低 5%。超過 55% 的電子設備失效的主要原因是溫度過高。對于 Si 基器件而言,其最高工作結溫為175℃。而要保證器件安全工作,民用級芯片的最高工作溫度不能超過 70℃、工業級芯片不能超過 85℃、軍用級則必須低于 128℃。溫度過高時,高密度集成微系統將主要發生熱失效。張大霖等人對 5G 車載網聯控制器進行仿真分析,發現當工作溫度達到 65℃ 時就必須對控制器進行有效散熱,否則就將面臨較大的熱失效風險。此外,過高的溫度還會導致系統內熱應力增加,對芯片造成損害。例如采用 FCOL 封裝時(如圖 1 所示),以銅做引線框架,銅的熱膨脹系數為 16.4×10-6/K,Si 為2.49×10-6/K。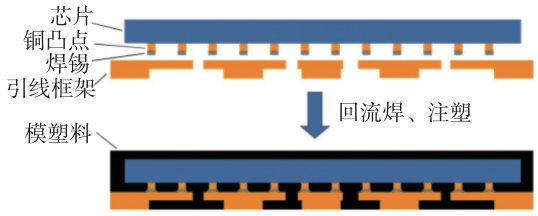
在大的熱載荷作用下,由于兩者熱膨脹系數差異大,將產生較大的熱應力,最終導致芯片產生裂紋、甚至完全失效。因此,如果不能進行有效散熱,熱量無法及時排出,將是高密度集成微系統失效的主要原因。為了更好的發揮高密度集成微系統的功能、提高其可靠性,對高密度集成微系統進行高效散熱至關重要。散熱通過熱量傳遞來實現,而熱量的傳遞方式主要有三種:熱傳導、熱對流和熱輻射。熱傳導是熱量從物體內部溫度較高的部分傳遞到溫度較低的部分或者傳遞到與之相接觸的溫度較低的另一個物體的過程,其本質是微觀粒子的熱運動,物質之間沒有宏觀位移和其他形式能量的轉化。傅里葉定律是描述其熱傳遞規律的方程,表達式為
(1)
式中的負號表示熱量傳導的方向與溫度梯度相反,Φ是熱傳導通量(W),k 是導熱系數(W/m·K),A 是垂直于導熱方向的截面積(m2),?t/?x為溫度梯度(K/m)。熱對流是流體中質點發生相對位移而引起的熱量傳遞過程。對流傳熱包括自然對流和強制對流。流體中的溫差造成密度的差別從而產生自然對流,而強迫對流則是用機械能使流體發生對流而傳遞熱量。當流動的氣體或液體與固體壁面接觸,且流體與固體之間存在溫差時,相互之間將發生熱量傳遞,這一過程稱為對流傳熱。對流傳熱是熱對流以及流體、固體中熱傳導過程綜合作用的結果,可以用牛頓冷卻公式來描述
(2)
式中,Φ 是對流傳熱量(W),h 是表面對流傳熱系數(W/m2·K),A 是壁面的有效對流換熱面積(m2),tw為固體表面的溫度(℃),tf為冷卻液的溫度。熱輻射是物體受熱引起內部原子激發,將熱能轉變為輻射能并以電磁波形式向周圍發射的過程。輻射出的電磁波遇到另一個能吸收該輻射能的物體時,輻射能將部分或全部被吸收又重新變為熱能。輻射傳熱不需要任何介質作媒介,可在真空中傳播。任何物體只要溫度高于 0 K,就會不斷向周圍空間進行熱輻射,但熱輻射量與物體溫度的四次方呈正比
(3)
式中,A為輻射面積,T為輻射體的熱力學溫度,σ為玻爾茲曼常數。對于電子器件/系統而言,其工作溫度低于 128℃,熱輻射量很低,熱量的耗散將主要通過熱傳導和熱對流實現。采用傳統方式封裝的電子器件/系統通常采用外置熱沉作為散熱器。從芯片到散熱器的熱傳導以及從散熱器到周圍環境的對流傳熱為主要的熱量傳輸方式。按散熱器帶走熱量的方式進行分類,電子器件的散熱可以分為主動散熱以及被動散熱。主動散熱包括強迫風冷散熱以及強迫液冷散熱等方式;被動散熱包括自然對流以及相變冷卻等方式。自然對流散熱技術是以空氣為傳熱介質,通過散熱器翅片周圍空氣的流動帶走熱量,是目前大部分低功耗電子器件采用的散熱方式。它的優勢在于結構簡單且運行可靠,自然對流散熱適用于熱流密度<10 W/cm2 的情形,而在高熱流密度場合它的應用具有局限性。為了提高散熱能力,可以使用強迫風冷散熱。其與自然對流散熱的區別在于它是使用風扇提供動力,迫使空氣流動。這樣空氣的流動速度可以大幅度提高,使散熱能力增強。強迫風冷散熱的散熱能力約為自然對流散熱的 5~10 倍。雖然它的散熱能力遠遠強于自然對流散熱,但仍然有限,不能滿足高密度集成微系統的需求。常溫下,空氣的導熱系數為 0.0267 W/(m·K),水的導熱系數約為空氣的 23 倍,導熱油的導熱系數約為空氣的 9.5 倍。為了進一步增強散熱能力,可以使用外置的強迫液冷散熱器,它的結構如圖 2 所示,在散熱結構中,熱源產生的熱量以導熱的方式傳遞給液冷板,然后通過對流傳熱的方式傳遞給冷液。冷液受熱后,在泵的作用下傳輸到換熱器上進一步散熱。
圖2 強迫液冷散熱典型結構
采用強迫液冷散熱,散熱效果明顯優于強迫風冷散熱。如果選用導熱系數更高的液體還可以進一步增強散熱能力。相比于水,液態金屬的換熱性能極其優異,例如鎵的熱導率約為水的 60 倍。因此,在同等情況下,使用液態金屬鎵作為冷液可以顯著提高熱量輸運能力。但是強迫液冷散熱也存在很多問題。首先它對液體管路的可靠性要求較高,此外強迫液冷散熱結構復雜,且系統的體積和重量也明顯大于風冷散熱,并不適用于高密度封裝的電子器件。利用材料相變的原理進行散熱稱為相變散熱,它可以分為直接相變散熱和間接相變散熱。直接相變散熱是指將元器件直接浸沒于散熱介質之中;間接散熱是指元器件和散熱介質不直接接觸。例如,熱管散熱就是一種利用液體相變的相變散熱方法,它的典型結構如圖 3 所示。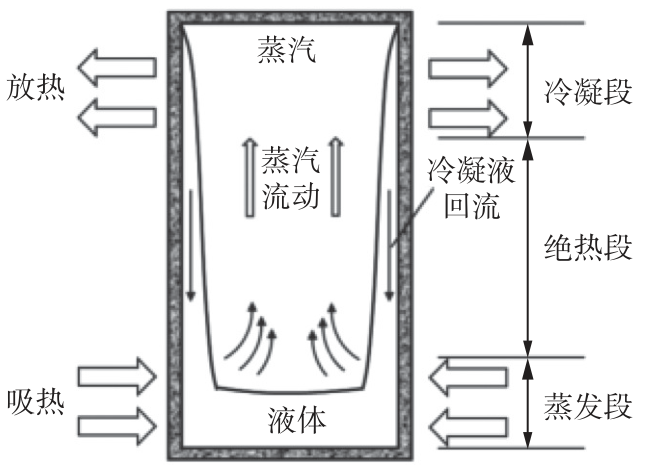
首先液體在底部的高溫側吸收熱量,然后液體汽化為蒸汽并到達頂部低溫側,通過管壁將熱量散出;蒸汽重新液化為液體,在重力作用下又回到高溫側,散熱過程不斷重復該循環。熱管散熱是目前筆記本電腦的主流散熱技術,但是它的散熱熱流密度一般為 10~100 W/cm2,傳統熱管在高密度集成微系統上的應用顯然是受到限制的。雖然風冷、液冷、相變散熱等傳統的散熱技術可以解決微電子領域很多的散熱問題,但是這些傳統的散熱方式都有一定的適用范圍。圖 4 和表 1 分別對比了不同散熱方式適用的熱流密度范圍及它們各自的優缺點。隨著電子設備向小型化、大功率、高集成化方向發展,電子器件的發熱功率也在不斷增加,傳統的散熱技術難以滿足相應的熱耗散需求,必須尋求更高效的散熱技術來加以應對。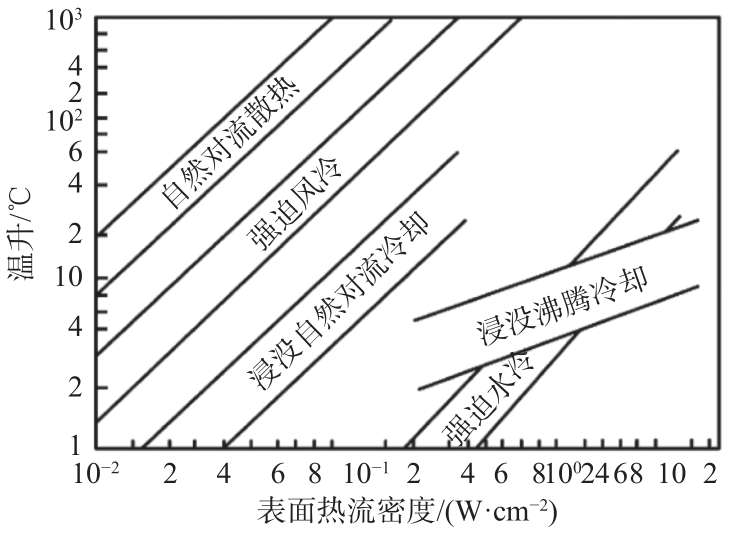
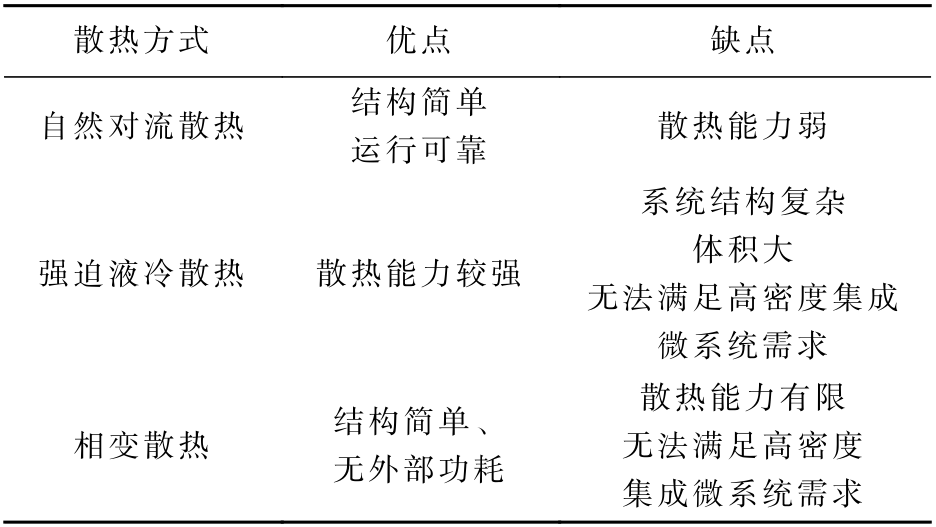
隨著集成度越來越高,電子器件/系統的平均熱流密度將達到 500 W/cm2,封裝體中局部位置的熱流密度甚至將高達 1000 W/cm2 以上。傳統風冷散熱熱流密度僅為 1 W/cm2,傳統液冷散熱的熱流密度也不超過 200 W/cm2。為了滿足高密度集成微系統的散熱需求,Tuckerman 和 Pease 在 1981 年首次提出了微通道熱沉冷卻技術。微通道熱沉的基本結構如圖 5所示。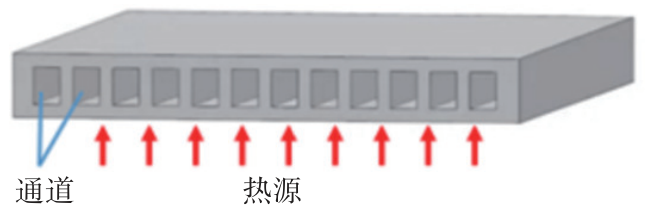
Tuckerman 和 Pease 采用濕法腐蝕工藝直接在Si 基板上刻蝕出寬 50 μm、深 300 μm 的多條平行微通道,之后在微通道中通入水作為冷卻介質,通過冷卻介質的強制對流達到高效散熱目的。散熱熱流密度可達 790 W/cm2。此時,基底相對于環境的溫升不超過 71℃,整體散熱基板的熱阻也低于 0.09℃/W。微通道熱沉散熱不僅可以實現很高的散熱能力,還可以實現散熱器與芯片的集成封裝制造。
圖 6 各類散熱技術對應的傳熱系數對比
與其他散熱方式進行比較,冷卻介質在微通道中流動散熱能夠達到更高的傳熱系數(如圖 6 所示)。而且,將微通道散熱器直接制作在芯片基板內部,可以保證芯片熱源到冷卻介質的傳熱路徑盡可能短,器件體積盡可能小,且散熱器制造工藝與傳統基板制造工藝兼容,適合高密度集成微系統應用,能夠在提高封裝體功能密度的同時降低成本。因此,微通道熱沉散熱技術在高密度集成微系統中有著巨大的應用前景。微通道散熱能力可以通過表面對流傳熱系數、努塞爾數以及散熱過程中單位面積能達到的最大熱流密度和綜合散熱性能系數等來進行表征。冷卻介質和微通道壁面的熱量傳輸是典型的對流換熱過程,該過程可以通過公式 (4) 來描述。公式(4) 中,對流傳熱系數 h 是控制和描述該對流換熱過程的關鍵。h 可以通過實驗進行測量,或者通過數值模擬的方式進行計算,其計算式為
(4)
式中tw和tf分別為微通道壁面與流體的平均溫度,q 為熱源產生的熱流密度。微通道中對流傳熱的強烈程度可以用努塞爾數Nu 來描述。Nu 越大,對流傳熱所占的比重越大。其計算式為
(5)
式中 l 為微通道的特征長度,通常可以取通道的水力直徑;λ為冷卻介質的導熱系數。對微通道內的單相流動進行分析可知,Nu 與流動狀態(可通過雷諾數Re來表征)、熱量傳輸與動量傳輸的相互影響(可通過普朗特數 Pr 來表征)以及微通道的結構和幾何尺寸(如通道特征長度 l)等有關。在實際工程應用中,往往通過基板單位面積上的最大熱流密度 q 和綜合散熱性能系數COP來評判基板內置微通道熱沉的散熱能力。綜合散熱性能系數COP定義為流體散熱功率Pextract與相應用于驅動微通道內流體流動所需的泵功率Ppump的比值
(6)
對于內置有微通道散熱器的基板而言,影響其散熱功率的主要因素是基板的熱阻 R
(7)
式中 Tt和Tb分別為沿傳熱路徑方向基板上表面和下表面的溫度。而泵功率則主要由微通道的流阻來決定。熱阻和流阻都很小的微流道散熱器,其綜合散熱性能高,而流阻和熱阻都取決于微通道結構和幾何尺寸。微通道結構對微通道散熱器的傳熱和傳質過程都有極大的影響。對微通道結構進行設計和優化需要考慮其拓撲結構、截面形狀/尺寸及層數等多方面的特征。微通道拓撲結構主要分為兩類。其中一類是以經典的平行直微通道為基礎逐漸發展起來的,這類微通道可以具有不同的延伸方式,如圖 7 所示,包括平直型、蛇形、螺旋型等。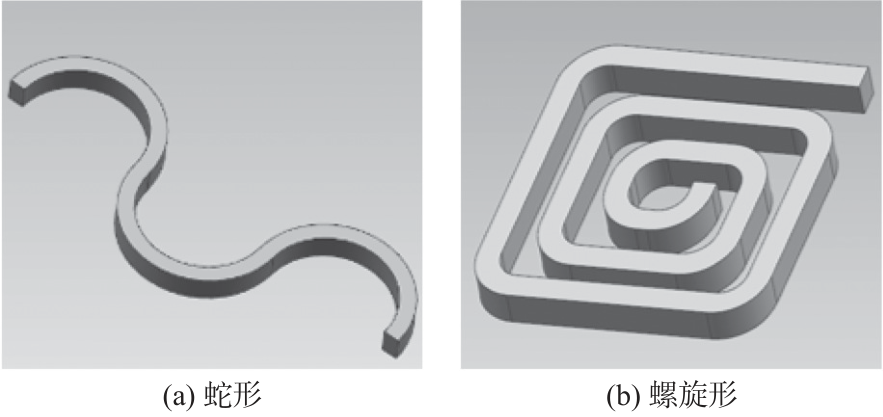
另一類是以自然界為模板設計的仿生拓撲結構,例如仿葉脈微通道拓撲結構、仿蜘蛛網微通道拓撲結構、仿河流網絡微通道以及仿蜂窩微通道等。它們的結構如圖 8 所示,通過數值分析的方法對不同的仿生拓撲結構進行分析,其熱仿真結果如表 2 所示。
除仿河流網絡微通道結構外,其他仿生拓撲結構與普通的平直微通道相比,散熱能力更強。同時,芯片發熱功率為 5 W 時,蜘蛛網型仿生拓撲結構與矩形平直拓撲結構相比,對應基板的最高溫度低 1.1℃;而當發熱功率為 40 W 時,蜘蛛網型仿生拓撲結構微通道基板的最高溫度比矩形平直拓撲結構微通道基板低 7.9℃。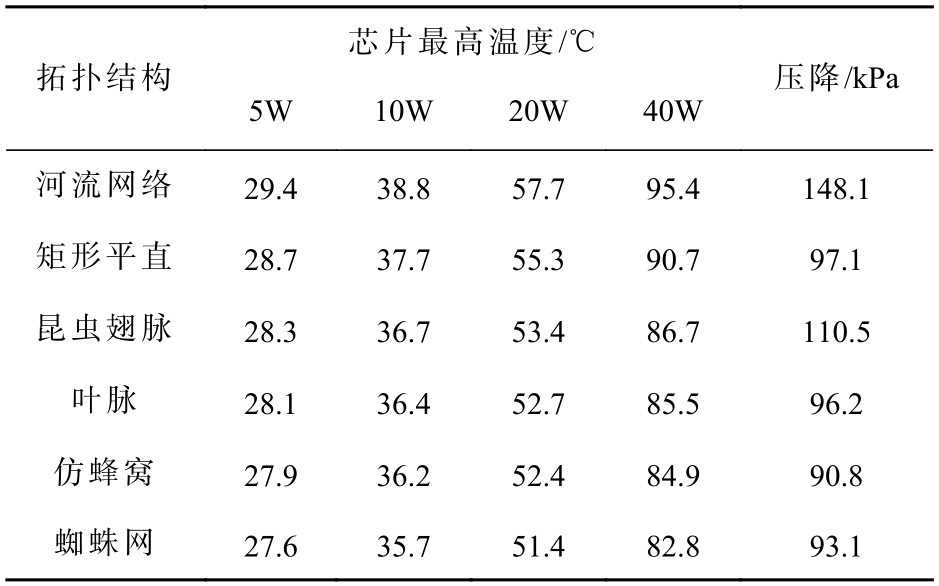
具有不同仿生拓撲結構的微通道散熱器散熱能力存在明顯差異。因此,用于高密度集成微系統時,必須針對實際情況對微通道拓撲結構進行優化設計。通常微通道截面形狀為矩形。有很多學者對矩形微通道進行了研究,通過建立矩形微通道的熱阻模型,對不同流動狀態下矩形微通道的熱阻特性進行研究。由結果可知,矩形微通道高寬比和其整體熱阻呈反向相關的關系,通道的高寬比越大,其整體熱阻越小。 進一步通過數值仿真的方法考察矩形微通道的對流傳熱能力,發現微通道的高寬比越大,則微通道內工質的軸向傳熱能力越強。在矩形微通道的基礎上,對截面為梯形的硅微通道進行研究發現當通道水力直徑在 51~169 μm范圍內時,沿流體流動方向,通道內的壓力梯度與摩擦系數均高于經典層流理論下的預測值。該研究還發現相同截面形狀的通道,微尺度下的流動阻力大于常規尺度下的流動阻力。對截面形狀分別為矩形、三角形以及梯形的微通道進行比較,冷卻介質流動的雷諾數 Re 在 100~1000 之間,水力直徑接近的情況下,矩形微通道的換熱系數最高,三角形微通道的換熱系數最低。此外,不同截面形狀的微通道在某些方面具有相似的規律,例如對截面形狀為矩形、三角形以及梯形的微通道而言,在橫截面積相等時,水力直徑小且高寬比大的微通道熱沉通常具有較小的熱阻和較大的壓降。除傳統的單層微流道結構外,一些微通道散熱器包含兩層甚至多層微流道。Vafai 等人比較了雙層與單層微通道的熱阻,發現雙層微通道熱沉比單層微通道熱沉具有更好的換熱效果。對內部結構分別為矩形微通道、單層波紋型微通道和多層波紋型微通道的三種微通道熱沉進行比較,可以發現在體積流率一定的情況下,單波紋型微通道的熱阻比直通道低;在同等情況下,雙層波紋型微通道熱沉的熱阻以及流動壓降都要小于單層波紋型微通道熱沉。通過結構優化,改進后的雙層波紋型微通道熱沉的散熱效果比普通的平直矩形微通道要好。此外,在這些雙層微通道的基礎上,建立了一種新型雙層交錯三角形凹穴微通道熱沉,與傳統的矩形微通道相比較,其 Nu 和摩擦因子 f 都高于傳統矩形直通道。其中 Nu 的提升可以表明,雙層交錯三角形凹穴微通道起到了良好的強化傳熱效果。f 的提升則是由于通道壁面凹穴的存在,使通道內產生了二次流,增大了主流流體的流動阻力。結合上述研究可知,合理設計多層流道可以有效增強對流傳熱,提升微通道散熱器的 Nu。此外,多層流道與單層相比,可以分別控制各層的流動方向和流動狀態,并調整微流道各部分之間流體的分配,可以更好地適應高密度集成微系統中存在多個分散熱源的散熱需求。隨著高密度集成微系統的發展,人們需要不斷提高微通道的散熱能力,而對其結構進行優化設計是顯著提升散熱能力的有效手段。對結構進行優化的原則是盡可能用最小的代價去獲得最優異的散熱性能。優化設計的評估準則主要包括熱阻、換熱系數、Nu以及泵功率等。微通道結構的優化設計通常利用數值模擬實現。由于在使用軟件進行數值模擬時。對于復雜的結構往往計算量很大,因此為了提高計算速度,逐步發展出了遺傳算法、多目標演算算法、排序遺傳算法以及共軛梯度算法等。例如采用簡化的共軛梯度法對雙層微通道熱沉進行優化,將流道的層數以及流道的高寬比作為變量,以整體導熱熱阻最小化作為目標,在泵功率一定的情況下,熱阻可以迅速減小并達到穩定最優值。通過結構優化增強傳熱傳質過程主要有兩種機制,一是利用某些特征結構增強對流動的擾動,二是增大換熱面積。能夠增強流體擾動的結構有很多,例如采用多層微流道、蛇形/波浪形/折線形微流道以及對微流道橫截面進行周期性闊縮等。但這些方法在增強流體的擾動、增強傳熱能力的同時也往往會使壓降增大。因此,對于這類結構的優化應該重點關注流阻的變化。增大換熱面積則主要通過改變通道橫截面形狀或拓撲結構來實現,例如采用 Ω 型截面通道結構或仿生樹形結構等。采用這些結構理論上可以增強溫度分布的均勻性或降低流阻,但是這些結構的制造加工往往非常困難。微通道熱沉內置于器件基板中,通常采用常規基板制造工藝來實現。例如,傳統平面工藝即可用于制造硅基板中內置的單層微通道,而 LTCC 為代表的基板制造工藝則可用于制造多層陶瓷基板中的單層及多層微通道結構。但現有工藝用于制造結構復雜的三維多腔體微通道結構時,仍然面臨一系列技術難題。首先,空腔的存在降低了基板的機械性能。這將導致加工過程中,局部懸空、轉折連接等位置處,容易由于溫度和受力不均,產生應力集中,出現裂紋、甚至塌陷。另外,人們還必須充分考慮到基板材料和宏/微觀結構對液體冷卻介質的密封能力以及對流體驅動壓力的耐受能力。以多層 LTCC 陶瓷基板為例,其制造工藝是一種基于粉末成型燒結的技術方法,基板內將不可避免地存在微納米尺寸的孔洞。且多層基板表面和內部存在大量金屬互連結構,多層瓷片之間的界面以及陶瓷-金屬連接界面處都有可能由于界面缺陷或界面異種材料間的熱、力性能失配,產生熱應力和應力集中,并最終形成裂紋。這些孔洞和裂紋都將導致液態冷卻介質的滲漏,大大降低電子器件/系統的可靠性。如何提高制造過程中基板多材料異種連接界面的連接強度、防止孔洞和裂紋的形核與擴展,是保證微流道熱沉散熱器正常工作的關鍵,也是其制造面臨的最大挑戰。除微通道結構外,通道內采用何種流體作為冷卻介質也會對微流道熱沉的散熱能力產生很大的影響。目前,微通道熱沉冷卻介質主要采用空氣、液態水、乙二醇以及液態金屬等。由表 3 可知,30℃ 下,水的導熱系數為 0.62 W/(m·K),高于乙二醇和導熱油,更高于空氣。它成本低,液態高純水性質穩定,粘度低,具有較好的導熱和流動性能,是最常用的微通道冷卻介質。表 3 常壓 30℃ 時傳統冷卻介質的物理參數對比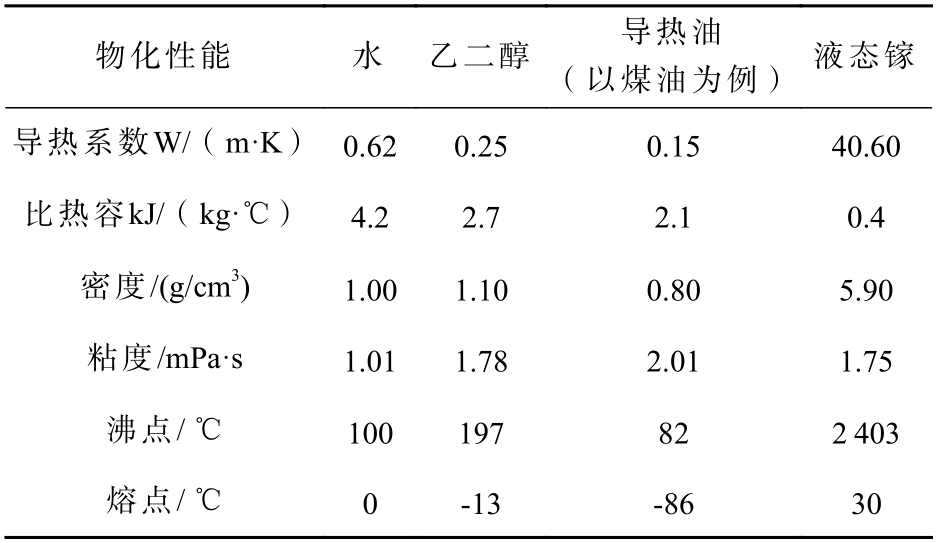
然而隨著高密度集成微系統的不斷發展,散熱功率越來越大、而水的沸點低且導熱系數有限,難以適應大功率器件/系統的散熱需求。為了進一步增強散熱能力和應用溫度范圍,有必要選擇性能更為優異的冷卻介質。相比于水,液態金屬的導熱能力極其優異,以鎵為例,其導熱系數約為水的 66 倍。在同等情況下,使用液態金屬鎵作為冷卻介質可以顯著提高熱量輸運能力且其沸點高,更適合用于高工作溫度下的散熱。但是液態金屬鎵的比熱容較小,比水低一個數量級,同時液態金屬的價格昂貴,粘度和密度大,使其應用受到較大限制。事實上,表 3所列的冷卻介質各有相應的應用溫度范圍和優勢,選用時需要進行綜合考量。自 Maxwell 理論發表以來,研究人員開始在液體中加入固體顆粒,以提高液體的導熱系數,從而提高液體的傳熱能力。加入的固體顆粒粒徑不斷減小,從毫米到微米,再到納米。1995 年,Choi將金屬納米顆粒成功分散于單相冷卻液中,所得多相混合液的導熱系數大幅度增加,由此也形成了“納米流體”的概念。納米流體是由液態連續相與納米尺度的固態分散相均勻混合形成的多相體系。連續相通常采用純的水、乙二醇等有機溶劑或液態金屬,也可以是上述多種液體互溶形成的混合溶液。而分散相則是金屬或金屬氧化物、碳等非金屬材料的納米粉體。通過控制連續相和分散相的材料種類、納米顆粒的尺寸、形貌等,即可調節納米流體的導熱系數、比熱容、粘度等性質,從而獲得綜合性能較優的冷卻介質。這使得納米流體成為熱管理領域近年的研究熱點之一。目前,納米流體的制備方法分為兩種,即單步法和兩步法。單步法是指在制備納米粒子的同時直接將納米粒子分散到基液中得到納米流體,如通過化學液相法等直接制備納米流體。單步法制備納米流體的優勢在于制備得到的納米流體通常分散性好、懸浮穩定性高。這主要是因為制備流程短,避免了額外的工藝過程,從而減少納米粒子的團聚。但是,單步法制備納米流體存在成本高、設備復雜、無法規模化生產等問題,并且此法一般難以控制納米粒子的尺寸分布和純度。兩步法是指先制備出納米材料粉體,再將納米材料以某種方式分散到基液中得到納米流體。兩步法制備納米流體設備簡單、成本低,同時,它幾乎適用于所有納米流體的制備,如不同基液的 Al2O3、TiO2等納米流體。兩步法最大的問題在于制備所得的納米流體穩定性一般不及單步法,容易發生團聚、沉降等現象。納米流體的“穩定性”通常指的是懸浮在其中的納米顆粒的濃度是否隨時間衰減。如果納米顆粒濃度隨時間不斷減小,說明納米流體向普通制冷劑(納米顆粒濃度為零)的方向不斷退化,其強化傳熱的效果也將逐漸減弱,導致它不能夠提供穩定的散熱效果。此外,若納米流體不穩定,顆粒團聚并在微通道壁面沉積,還會造成微通道局部流動阻力增加。如果流體驅動力不足,沉積越來越嚴重,甚至會導致微通道堵塞。納米流體不穩定的原因主要是由于納米顆粒比表面積大,導致其表面原子比例增多、原子配位不足、納米顆粒的表面能高,分散在連續相中后,納米顆粒之間相互碰撞容易結合,進而形成尺寸較大(通常是亞微米甚至微米尺度)的團聚體,降低表面能。團聚過程加速了顆粒的重力沉降,致使納米流體無法保持穩定。影響納米流體穩定性的因素主要有顆粒濃度、顆粒表面狀態、分散劑(表面活性劑)、溶液pH 值、工作溫度等。通常兩步法制備過程中需要在基液內加入一定濃度的表面活性劑,通過電磁攪拌、超聲震蕩等方法促使納米顆粒更好地均勻、穩定分散于基液中,并控制混合液的 pH 值,使納米流體保持較為穩定的狀態。制備過程中增強納米流體分散均勻性和穩定性的方法如圖 9 所示。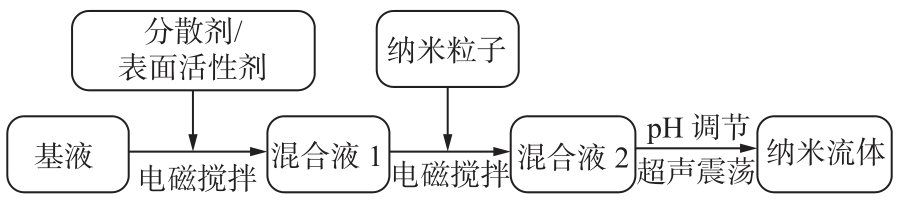
圖 9 納米流體兩步法制備過程及分散穩定性控制方法目前,評價納米流體分散穩定性主要通過沉降實驗、Zeta 電位測量和紫外可見分光光度測試等方法。沉降實驗主要是目測,觀察一定時間內重力作用下,納米粒子在基液中的沉積量。若無明顯分層和團聚現象,則可認為納米流體的穩定性較好。此法簡便、直觀。Zeta 電位是表征納米流體穩定性的重要指標,其絕對值越大,粒子間的靜電排斥力越大,穩定性越好。通常認為其絕對值大于 30 mV 時,納米流體具有較好的穩定性。紫外可見分光光度測試可以獲得納米流體的吸收光譜并確定最大吸收波長處的吸光度值,若吸收光譜和吸光度不隨時間變化,則納米流體的穩定性好。納米流體作為冷卻介質在微通道散熱領域的應用前景非常巨大,但是就現有的研究而言,納米流體的實際應用仍然面臨兩大難題。其中最主要的問題就是納米流體的穩定性問題,尤其是在微通道內低維空間尺度下,納米顆粒之間以及納米顆粒與微通道壁面之間的碰撞頻率將大大增加,導致納米顆粒團聚;且在此條件下納米流體穩定性對溫度也更加敏感,將導致納米流體穩定性控制更加困難。此外,納米流體的導熱系數、粘度等物化性質也容易受到納米顆粒碰撞和團聚的影響,難以準確測量和表征,導致其傳熱傳質特性難以預測和控制。目前,相關文獻報道的相關數據存在較大差異。未來研究的重點一方面是實現納米流體的長期分散穩定并增強傳熱特性,另一方面則需要通過建立合適的模型,揭示其傳熱傳質機制,從而對其傳熱傳質特性進行較為準確的預測。與傳統的散熱技術相比,微通道熱沉散熱技術直接利用器件基板加工技術將微通道散熱器直接制造在基板內,可以方便地實現散熱器的集成,且散熱路徑短、散熱能力強,特別適用于高密度集成微系統的熱管控。微流道散熱器的傳熱和傳質特性可以通過對流傳熱系數 h、努塞爾數 Nu 以及綜合散熱性能系數COP等來表征。微通道的拓撲結構、截面形狀/幾何尺寸、層數以及微通道中冷卻介質的物化性質和分散穩定性都將對傳熱傳質過程產生重要影響。對微通道結構和冷卻介質性質進行優化設計是提高微通道散熱器綜合散熱性能的主要手段。根據近期的報道,單片集成的岐管式微通道散熱結構可以水為冷卻介質,在 0.57 W/cm2 的的泵浦功率下實現熱流密度高達 1700 W/cm2 的散熱,平均努塞爾數達到 16,充分展示出微流道散熱技術在高密度集成微系統熱管理領域的廣闊應用前景。而納米流體作為一種新興的散熱冷卻介質,將有望在現有基礎上,進一步增強微通道散熱器的傳熱傳質能力。目前,在復雜三維微通道結構及高穩定納米流體的制備和應用中還存在諸多問題,深入研究相關制造工藝技術和傳熱傳質機制,對于微流道散熱技術在高密度集成微系統熱管理領域的實際應用至關重要。
標簽:
導熱散熱 點擊:
版權聲明:除非特別標注,否則均為本站原創文章,轉載時請以鏈接形式注明文章出處。