來源:科學通報,中國知網
作者:丹聃, 姚程寧, 張揚軍, 錢煜平, 諸葛偉林
摘要:電池熱管理是發展高性能動力電池系統的關鍵技術之一,也是工程熱物理領域研究前沿和熱點。本文介紹鋰離子動力電池熱特性,闡述熱管理對動力電池的重要性。介紹動力電池熱管理主要技術手段,重點介紹熱管技術應用于電池熱管理的研究現狀,從電池運行工況對系統傳熱的影響研究、熱管傳熱特性分析與設計、熱管理系統散熱結構設計與傳熱分析及采用熱管的電池加熱研究4個方面闡述當前基于熱管技術的電池熱管理研究現狀。最后,總結當前研究存在的不足及需要突破的關鍵問題,以期促進先進動力電池熱管理系統開發。
關鍵詞:鋰離子電池,熱管理,熱管,強化傳熱,低溫加熱動力電池是電動汽車的重要組成部分,其性能優劣直接制約整車動力性、安全性和經濟性。動力電池能量密度決定電動汽車續駛里程,功率密度決定最大爬坡度及最高車速,循環壽命和成本影響整車成本和使用經濟性,動力電池的電/熱安全性和環境適應性,是決定電動汽車整車安全性和環境適應性的關鍵因素。鋰離子電池是鎳氫電池等的升級換代,具有較高的能量密度(約250?W?h/kg)和功率密度(約1500?W/kg),在續航里程和使用壽命等方面具有較強優勢,為當前研發和產業化的重點。
鋰離子電池系統是具有復雜流動和傳熱過程的電化學動力源,溫度是影響其性能的關鍵因素,主要體現于三方面: (1) 溫度升高,加劇電池容量衰退,過高的溫度甚至造成熱失控;(2) 溫度過低,電池功率、容量顯著衰減,充放電效率下降;(3) 電池組中不同電池之間溫度差異,會導致單體內阻、容量的不一致性和不均速老化,形成整個電池系統性能與壽命短板。因此,動力電池工作性能在較大程度上受到溫度影響,需通過設計合理的熱管理系統結構、開發先進的熱管理控制策略,使動力電池工作在適宜溫度范圍內,并有效控制單體間溫差,從而提高動力電池性能。本文首先介紹鋰離子電池產熱機理以及溫度對其性能的影響,說明電池組熱管理的重要性及熱管理系統設計要求;對常見熱管理技術手段進行闡述,指出熱管技術的優勢并重點介紹基于熱管技術的電池熱管理研究;最后,提出基于熱管技術的電池熱管理研究中需解決的關鍵問題及研究展望。
01 鋰離子電池產熱特性與熱管理需求
鋰離子電池充放電過程本質是離子遷移與化學反應,Li+在層狀結構碳材料和金屬氧化物內嵌入和脫出,如圖1所示。正常工作條件下,電池產熱來源包括歐姆熱、電化學反應熱和極化熱。隨著溫度升高,電池內部發生一系列放熱化學反應,包括電解液分解、負極熱分解、負極與電解液的反應、SEI膜分解反應等,過高的溫度可能導致熱失控,不同溫度下電池內部發生的反應如圖2所示。
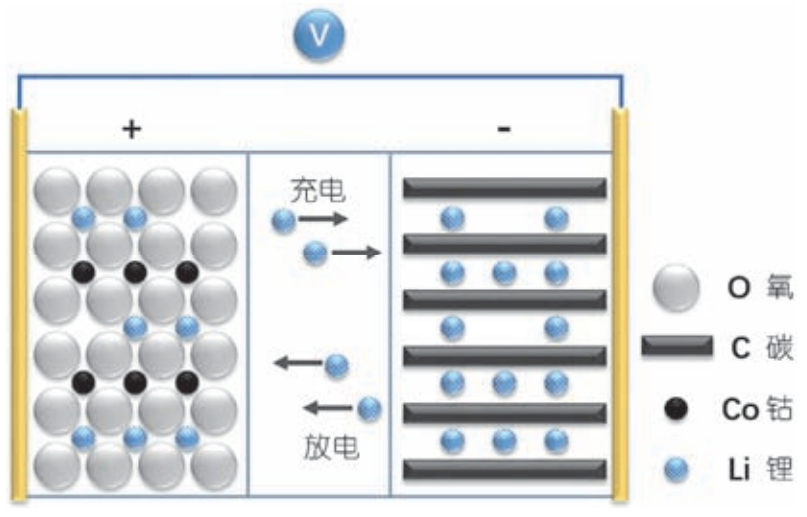
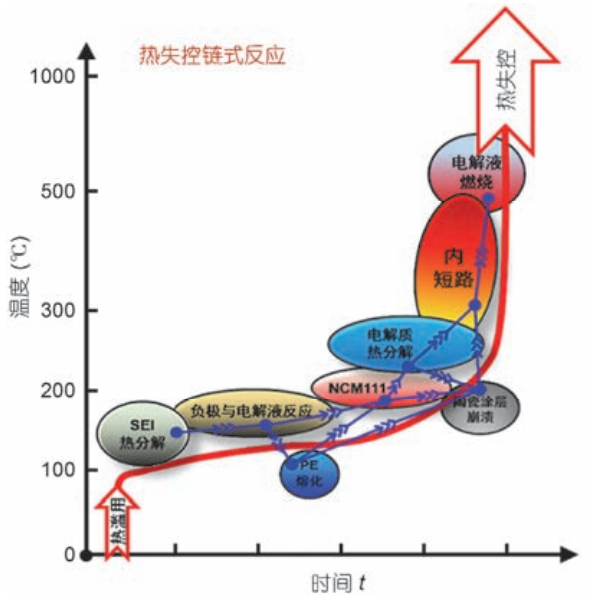
圖2 不同溫度下鋰離子電池內部電化學反應
溫度引起電化學性能變化,從而影響電池使用性能與壽命。溫度升高,電化學反應速率增加,加劇電池容量衰減; 低溫環境也會造成電池性能衰減,鋰離子在電極活性物質中的遷移能力減弱,充放電容量迅速下降。此外,過高或過低的溫度會加速電池老化,影響電池壽命。特別在大倍率充放電情況下,溫度對電池壽命的影響更為顯著。研究表明,索尼18650鋰電池在25°C循環工作800次后容量損失為30%,而在50°C循環工作800次后容量損失接近60%。過高或過低的存儲溫度也會導致鋰電池容量衰減,加速老化。車用電池系統通常由成百上千節電池單體組成,電池組面臨更加嚴峻的熱問題。受傳熱結構、串并聯方式、運行工況等因素影響,電池組內各單體電池溫度在運行過程中呈現較強不一致性,從而導致電池內阻、容量衰減和放電深度不一致,進而導致整個電池組可用容量和壽命衰減(圖3)。
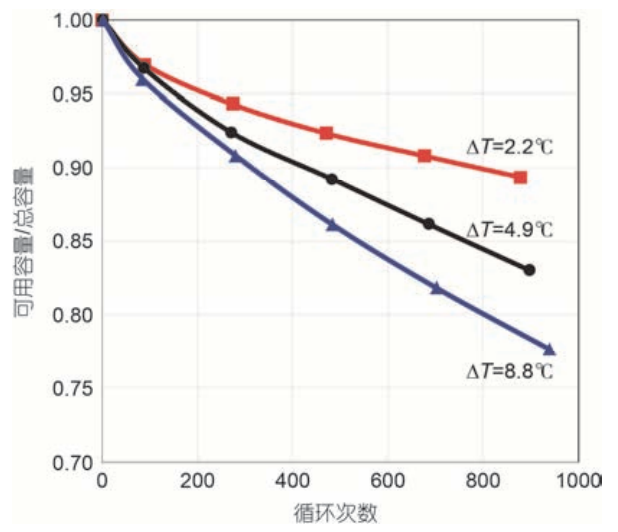
實際上,電芯溫度一致性是決定電芯壽命利用率的重要參數,進而影響電池組壽命(式(1)),因此,保證電芯溫度一致性尤為重要。綜上所述,控制動力電池組溫度,減小單體電池間溫差對提高電池組性能具有重要意義。目前認為鋰電池最佳工作溫度范圍為25~40°C,單體間溫差小于5°C。當前熱管理技術大多以上述溫度和溫差為目標,對熱管理系統結構與控制方法進行設計,保證動力電池組工作效率與使用壽命。
電池熱管理包括高溫散熱與低溫加熱。常用的電池散熱手段包括基于氣體(空氣)、液體、固體相變材料(phase change material,PCM)和熱管的電池散熱技術。電池模組的低溫加熱手段主要包括基于流體或熱敏電阻元件(positive temperature coefficient,PTC)的外部加熱和基于電池自身產熱內部加熱方式。應用空氣主要包括強制對流和自然冷卻。研究者通過冷卻風道結構設計、電池排列方式設計、通風控制策略優化等方法研究了電池組傳熱特性并提出強化傳熱及改善均溫性的措施。由于風冷系統具有低成本、系統結構簡單、便于維護等優點,被應用于一些續航里程較短且主打性價比的車型上,如日產LEAF采用被動式電池熱管理系統為其鋰離子軟包電池組散熱,此外,豐田普銳斯、起亞Soul EV、上汽榮威MARVELX也均采用風冷散熱。然而,對于大規模鋰離子電池組而言,由于電池熱負荷較大,熱傳導的弛豫時間較長,空氣冷卻無法滿足散熱要求。尤其是在高溫環境下,風冷熱管理技術換熱效率較低,且不一致性較大,難以滿足熱管理需求。由于空氣對流換熱系數較低,采取液體代替空氣成為強化傳熱的必然手段,研究通常在電池組底部或單體之間布置液冷板進行散熱。目前液冷系統的研究大多集中于冷卻通道的設計: 通過增加冷卻液通道個數、改善冷卻通道結構、在通道內布置翅片、設計連通式組合冷板等方式改善散熱能力和均溫性。近年來,采用新型制冷工質作為熱管理冷卻劑的研究也較為普遍,如采用液態金屬、納米金屬流體等實現強化散熱。當前,不同車企對于液冷散熱應用方式不盡相同,特斯拉液冷系統采用質量比為1:1的水和乙二醇混合冷卻液,將冷卻管道蜿蜒布置在18650電池堆中,對每節電芯進行散熱; 雪佛蘭Volt軟包電池模組也采用液冷散熱,如圖4所示,每兩節軟包電芯構成一個單元,將一塊帶有液冷流道的鋁板布置在兩節電芯之間,采用并行流道設計方案,實現每節電芯大面積冷卻。此外,還有基于液體相變原理的電池散熱方法,即將空調系統蒸發器安裝在電池系統底部,利用制冷劑蒸發帶走電池產熱,也稱直接冷卻,典型的應用如寶馬i3系列。液冷熱管理是當前工程應用中較為普遍的方式,然而系統較復雜、質量較大,同時存在泄漏可能。
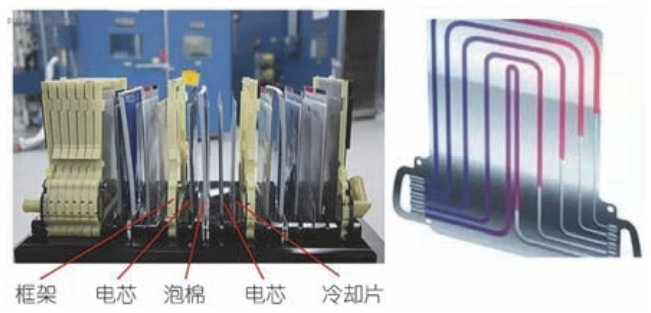
基于固液相變材料的電池熱管理是當前另一研究重點,其原理是利用PCM相變吸熱降低電池溫度。PCM可有效保證電池組均溫性,然而材料導熱性能較差,因此當前研究主要集中于PCM材料制備和改善其導熱性能。此外,PCM質量較重,降低了電池包能量密度,以上原因限制了相變材料在動力電池熱管理中的應用。
鋰離子電池在低溫環境下充放電性能顯著下降,因此,需要對電池進行預熱,改善其使用性能。當前的加熱技術主要分為內部加熱與外部加熱兩類。內部加熱指電池通過其內阻產熱的升溫方式,包括外加交流電加熱、電池之間互相脈沖充放電加熱以及電池自放電加熱。此外,Wang等人設計了一種三電極電池,增加鎳電極并通過電極切換實現快速電池的快速加熱啟動。外部加熱主要包括空氣加熱法和液體加熱法。前者采用電熱絲加熱空氣進而加熱電池,溫度均勻但能耗較高。后者通過加熱流道內的液體進而給電池組加熱,結構較復雜且升溫速度較慢。除上述基于對流的加熱方式,亦可采用PTC或小功率加熱膜直接對電池表面進行加熱,該方式對電池散熱造成一定影響。此外,也有利用PCM吸熱/放熱原理對電池進行熱管理的方法。
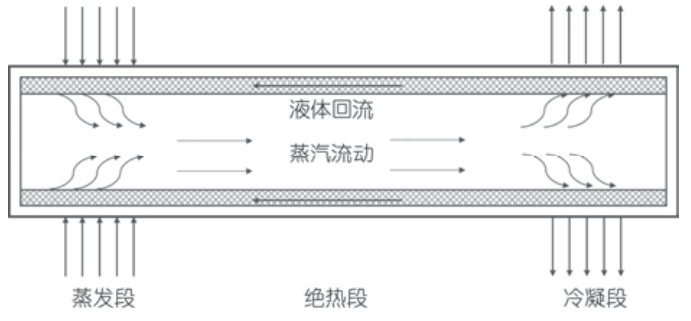
圖5 熱管工作原理示意圖
采用熱管作為電池高溫散熱/低溫加熱的傳熱元件是一種新型熱管理方式。熱管是基于氣液相變原理傳熱的高效換熱原件,工作原理如圖5所示。液體工質在受熱端蒸發汽化,在壓差驅動下流向另一端并在冷凝段凝結放熱,液體工質通過毛細力沿多孔材料返回蒸發段,具有傳熱效率高、均溫性好等優點。
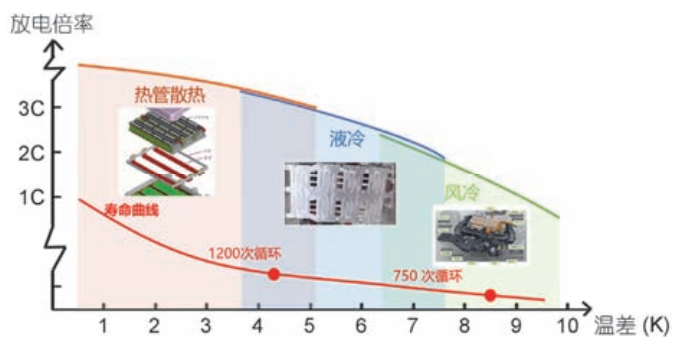
圖6 基于風冷、液冷及熱管的熱管理系統性能對比示意圖
熱管當前已被廣泛應用于能源化工、航天航空、電子電力等領域。在電池熱管理領域,熱管在散熱/加熱速率、電池組均溫性方面均有較強優勢(圖6)。高溫散熱方面,相比于強制風冷,通過熱管導熱再進行風冷換熱的方法可使電池溫度降低20°C以上(20?Ah方形電池,5C放電); 低溫加熱方面,基于熱管導熱的電池升溫速率較PTC直接加熱提高1.5倍。特別在大電流充、放電工況下,熱管展現出更加優越的傳熱性能和均溫性。熱管的應用有助于實現未來高性能電池包的研發,近年來受到廣泛關注。
圖7為典型的采用熱管作為傳熱部件的電池熱管理系統示意圖。各單電池充放電過程中產生的熱量,直接(或通過鋁板等導熱介質)傳遞給布置在單體側面或底部的熱管,再由熱管冷端的散熱系統將熱量帶走。由圖可見,影響系統傳熱性能的主要因素包含三方面: (1) 動力電池運行工況與產熱,即熱源工作條件對熱管理系統性能的影響; (2) 熱管的傳熱特性,主要涉及熱管內部結構設計及其在動力電池組中的布置方式對系統散熱性能的影響; (3) 熱管冷端散熱,主要包含直接風冷與水冷二次換熱兩種形式。此外,在低溫情況下,需要通過PTC或電加熱膜對熱管進行局部加熱,再以導熱形式傳遞給電池,這部分研究涉及加熱系統設計和加熱策略研究。
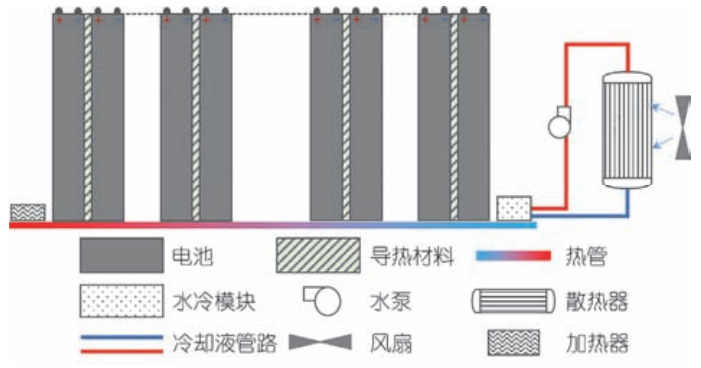
圖7 基于熱管的電池熱管理系統示意圖
系統運行工況決定電池產熱特性,是影響系統傳熱的關鍵因素。電池溫度升高至熱管啟動溫度之前,熱管以管殼導熱的形式傳遞熱量,當溫度上升至啟動溫度,管內工質開始利用相變潛熱吸熱,從而增大其導熱系數,使電池溫度逐漸趨于穩定。研究表明,電池在恒倍率放電情況下從初始放電至溫度達到穩定所需時間約400~2000s,與電池放電倍率、熱管冷端散熱條件等因素有關。電池產熱率隨放電倍率非線性增加,一節10?Ah方形電池在3,5和8C倍率下的產熱率分別約10.5,25.4,54.4?W,熱源條件的變化導致熱管熱阻不同,達到穩定時溫度分布也不同。此外,冷端換熱量越大,熱管達到穩定所需的時間越短且穩定溫度越低。電動汽車運行環境復雜多變,隨時面臨加速、滑坡、急剎等情況,動力電池熱特性與穩態工況有較大不同。圖8給出了穩定和非穩定運行工況下電池溫度及溫差變化規律的差異。Tran等人采用時變發熱功率模擬車用行駛工況,比較了翅片風冷和基于熱管的翅片風冷兩種情況下發熱模塊溫度波動情況,表明采用熱管耦合翅片風冷的電池溫度較低,且溫度波動相對較小,然而在變化過程中,溫度與熱流密度變化趨勢并非一致,受到熱慣性的影響,產熱率突降而溫度繼續升高隨后降低。
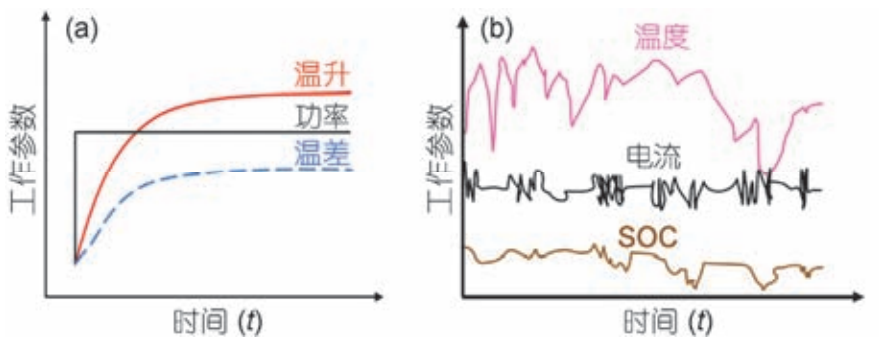
圖8 車用工況電池溫度變化示意圖. (a) 穩定工況;(b) 非穩定工況
上述研究從單體層面探討了非穩定工況對電池帶來的影響以及熱管的可靠性。電池成組后的動態傳熱特性與單體電池有較大差異,特別是熱管理結構對電池組內溫差的影響較為明顯。電池組溫升和溫度分布與熱管理系統的動態傳熱過程密切相關,當前研究尚處于傳熱效果驗證階段,如何結合電池組運行條件,對熱管理系統制定有效的實時控制策略,從而實現高效、低能耗的電池熱管理,是需要進一步解決的問題。
3.2 熱管傳熱特性分析與設計研究
3.2.1 基于動力電池的熱管設計與優化
熱管設計是影響傳熱性能的重要因素,其換熱效果與通道尺寸、吸液芯結構、充液率等因素密切相關,合理的熱管設計對提高電池熱管理效率十分重要。由于動力電池產熱的特殊性,許多學者在針對電池的熱管設計方面展開研究。Jang等人研究了不同工質對回路型重力熱管換熱性能的影響,當電池發熱量為50?W時,以丙酮為工質可控制電池平均溫度低于45°C,優于以水為工質的散熱效果。Putra等人發現工質散熱效果與電池產熱率密切相關,針對不同的熱源發熱量,采用不同工質才能發揮熱管的最大功效,當電池產熱率大于1.61?W/cm2時,采用乙醇做工質的換熱效率最高。Chi等人研究了充液率對脈動熱管換熱的影響,發現熱管的最佳充液率隨著電池產熱率的增大而提高。因此,需要針對熱源條件選擇適當的工質種類及充液率,以達到最佳換熱效果。當前研究大多從工質層面(工質種類、充液率)研究和優化熱管用于動力電池的傳熱特性,也有少數文獻從結構角度對熱管性能進行改善。Swanepoel設計了基于脈動熱管的電池熱管理系統,分析了介質和管道寬度對熱管傳熱性能的影響,發現當熱管內工質為氨水時,熱管寬度需小于2.5?mm,才能保證其在電池熱管理中的啟動及散熱效率。在現有動力電池熱管理研究采用了不同種類的熱管,如重力型熱管、燒結熱管、脈動熱管、平板環路熱管、平板微熱管等,尚無統一的選型或設計方法。從結構形式上看,平板類型熱管在動力電池熱管理系統中展現出優越性,有望成為動力電池熱管理的首選,然而當前針對平板熱管的設計研究較少。
3.2.2 熱管布置方案設計
電池熱管理系統布置方式是影響熱管導熱性能的另一關鍵因素。Tran等人對比了水平與垂直放置時熱管導熱性能。施加38?W熱源模擬電池包產熱,水平布置時熱管蒸發端溫度達到61°C,垂直布置時溫度僅51°C。饒中浩采用脈動熱管進行實驗也得到類似的規律,搭建了如圖9所示的電池熱管理實驗測試平臺,實驗表明在相同產熱功率下,豎直放置時電池表面溫升較小,且局部溫差比水平放置時更小。
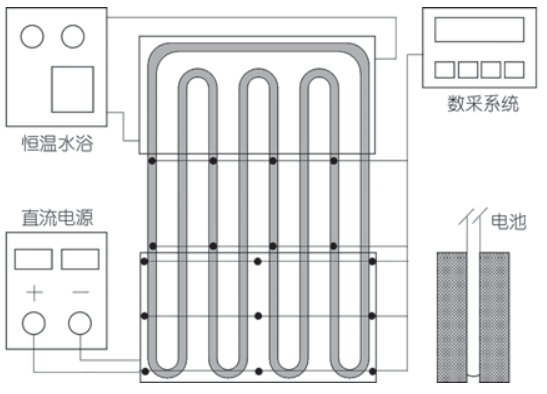
此外,裝置傾斜角度也對傳熱造成影響。熱管水平安裝時,電池表面溫差受傾斜角度影響較大; 而熱管豎直安裝時,重力與毛細力雙重作用降低熱管傳熱阻力,路面坡度對局部溫差幾乎無影響。上述研究均說明熱管豎直布置時的散熱及均溫效果優于水平布置方式。Wang等人在熱管豎直布置方式下研究電池擺放方向對熱管傳熱效果的影響,表明管內工質可迅速將高溫端(電極)熱量傳遞至冷凝端,相同產熱功率下電極朝上的方式可延緩溫度上升時間。為保證熱管傳熱性能的發揮,電池熱管理系統結構設計應充分考慮熱管布置方式對其導熱性能的影響。
3.3 熱管理系統散熱結構設計與傳熱分析研究
作為電池熱管理傳熱部件,熱管吸收電池產熱的同時需快速將熱量散掉,以保證其在電池組中正常工作。通常情況下,熱管冷端可采用風冷和水冷散熱兩種方式,前者結構簡單,易于實現,后者結構相對復雜,但在散熱需求較大時表現出更好的性能。
3.3.1 冷端風冷散熱
熱管冷凝段采用直接風冷是最簡單的散熱方式。Ye等人對熱管冷端進行強制風冷散熱,可使電池(LiFePO4,18?Ah)在1C放電條件下維持在35°C以下,若冷端采用自然冷卻,放電末期溫度高于40°C。為強化熱管散熱能力,可采用增加冷端翅片數目、改善冷端翅片設計、提高風冷流速、增大冷凝段長度等方式。熱管根數、翅片個數、翅片間距對散熱效果也有重要影響。在一節電池表面布置多根熱管可強化散熱,但由于冷端沿氣流方向平均換熱系數越來越低,增大了電池表面溫度不均勻性。通過在第一根熱管前布置擾流圓管(圖10(d))可提升電池表面溫度均勻性。
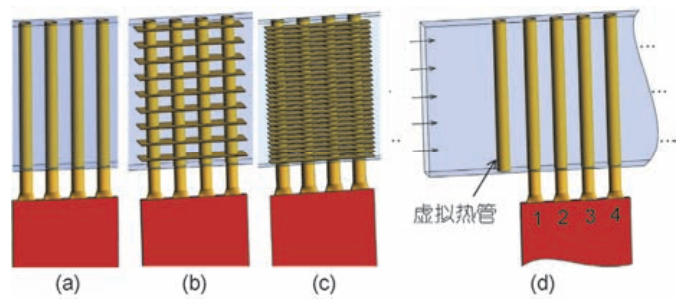
圖10 熱管冷凝段設計方案. (a) 冷凝端為光管; (b)翅片間距 10 mm; (c) 翅片間距 3 mm; (d) 散熱端帶有一根虛擬熱管許多研究者采用熱管與相變材料耦合散熱方式提升電池表面均溫性,將PCM附著在電池表面,熱管嵌入PCM中帶走熱量,冷端采用風冷散熱,圖11是一種典型的熱管-PCM耦合風冷散熱系統,該結構可保證電池組2C放電結束后最大溫差低于2°C,且冷卻風速會影響電池最高溫升。
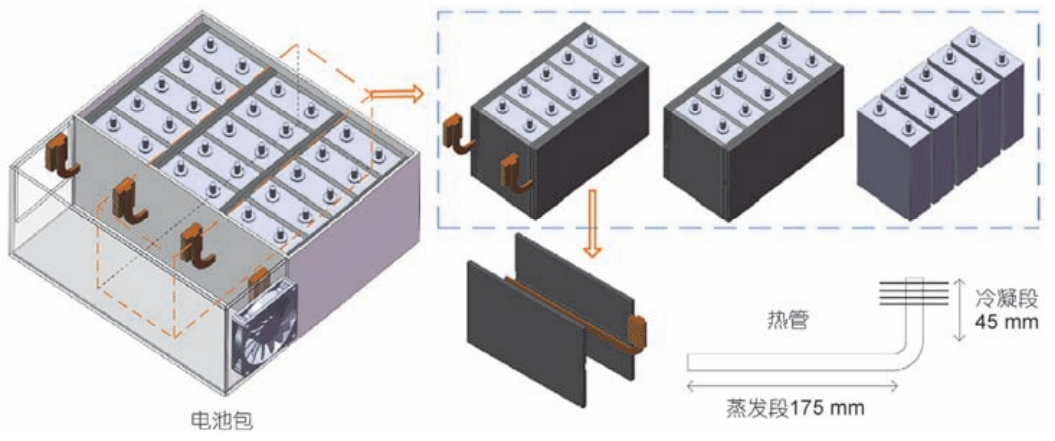
圖11 方形電池熱管-PCM耦合熱管理系統
增大冷凝段長度是提升熱管散熱能力的另一有效途徑,然而冷凝段長度增加會導致電池組溫差增大,為同時保證電池組溫升和溫差,并考慮電池組空間布置等實際因素,熱管冷凝段長度存在最佳值。
3.3.2 冷端液冷散熱
由于空氣比熱容較低,采用熱管與液冷耦合散熱可彌補空氣冷卻的不足。根據熱管冷端與液體流道接觸方式,可分為接觸式液冷換熱和非接觸式液冷換熱。接觸式液冷系統如圖12所示,熱管冷端浸泡在水槽中,內部通入一定流速液體,2C持續放電半小時后電池溫度不超過42°C,說明熱管與液冷耦合散熱效果。
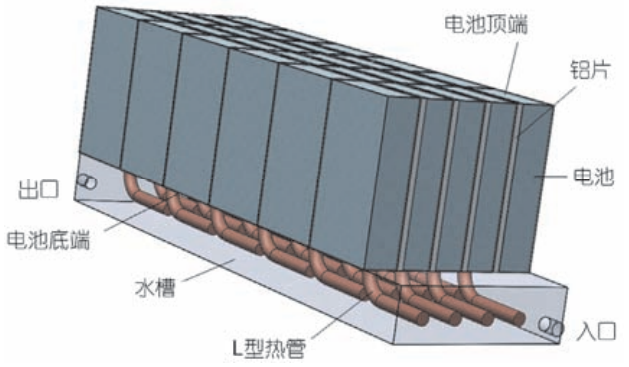
Zhao等人采取冷端噴水提升電池散熱效率,每兩節電池之間布置一根平板微熱管并向其表面以一定頻率噴水,電池在2C持續放電工況下溫升僅為4°C,3C放電工況溫差小于2.5°C。
非接觸式液冷系統通常將熱管排布在電池表面,通過液冷流道與熱管冷端接觸帶走熱量,熱管冷端并非直接浸泡在冷卻液中,安全性較高。奧迪公司設計了如圖13所示的電池熱管理方案,在每兩節電池之間布置一塊銅板,并將4根燒結熱管嵌入銅板內,最后通過貼在熱管冷端表面的液冷板將熱量帶走。在400W電池產熱功率條件下,該系統可維持電池溫度在50°C以下,具有較好的冷卻效果。
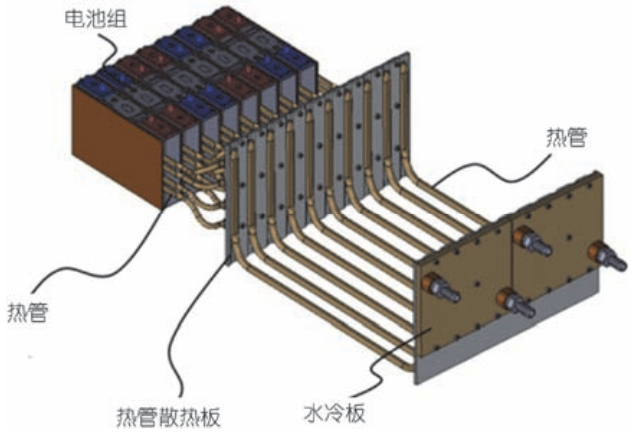
圖13 動力電池熱管散熱設計方案
當前大部分研究以電池的溫升和溫差作為考核指標,然而,強化傳熱帶來更多系統能量消耗及重量增加,較少從系統層面進行設計考量。如何兼顧電池放電特性、散熱效果以及系統能耗和輕量化等指標,提出熱管理系統高效散熱方案,是將來在電池強化散熱方面的研究重點。如前文所述,低溫環境下鋰離子電池充放電效率大幅衰減,目前采用熱管作為傳熱部件的低溫加熱研究引起廣泛關注。Ye等人采用微平板熱管布置在電池表面,另一端采用加熱元件加熱(圖14),電池從-10,-20,-30°C升溫至0°C所用的時間分別為350,780,1100s,溫升速率是傳統底部加熱方式的1.5倍。加熱過程中溫差可控制在3°C以下,遠低于傳統加熱方式(9°C)。梁佳男等人發現提高加熱功率可提升電池升溫速率,但同時增大電池表面溫差,因此需要綜合考慮加熱時間和電池溫差,以確定最佳加熱策略。
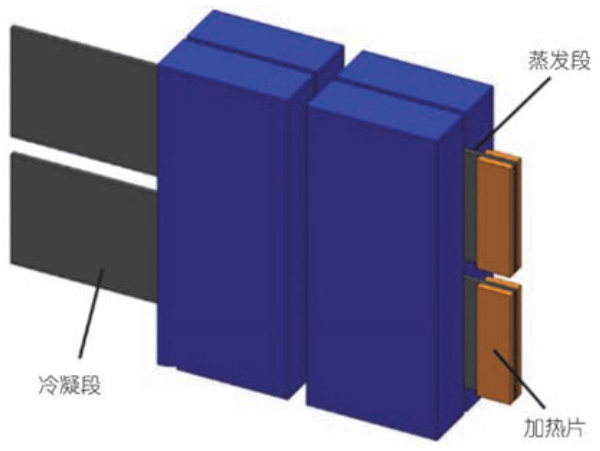
圖14 基于熱管的鋰離子電池加熱結構示意圖
Zou等人設計了如圖15所示的熱管-液體耦合綜合熱管理系統,既可實現電池低溫加熱也可以用于高溫冷卻。管道內的制冷劑經過PTC加熱,然后通過熱管將熱量傳遞給電池。在加熱的初始階段電池溫升較快,隨著熱管的冷、熱端溫差逐漸減小,換熱能力減弱,最終換熱量趨近于定值,約900?s后電池溫度上升至20°C。
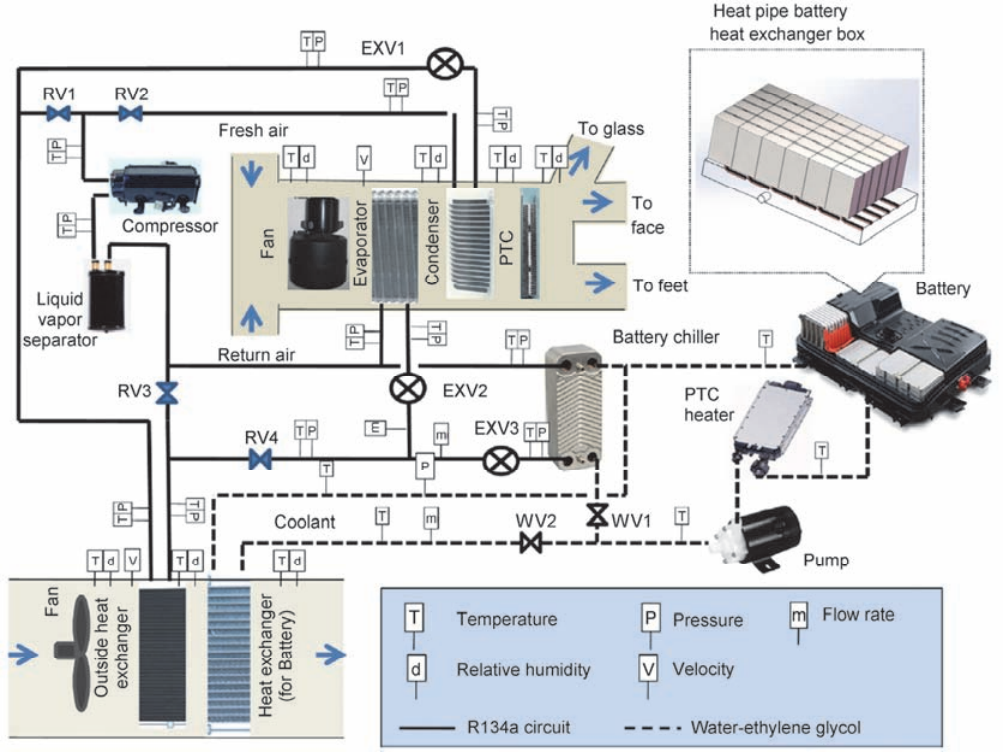
圖15 熱管加熱系統示意圖
當前基于熱管的電池加熱系統通常采用傳統熱管或微通道熱管布置在電池表面,另一端采用熱水加熱或PTC加熱,研究大多處于實驗驗證階段,現有研究結果充分展示了采用熱管加熱的高效性和均溫性,進一步的研究應圍繞低溫加熱策略展開。溫度是影響動力電池性能的關鍵因素,高效熱管理系統對電動汽車具有重要意義。熱管具有較強的換熱能力和均溫能力,是未來電池熱管理系統的重要研究方向。采用熱管作為電池散熱/加熱元件的研究已經取得顯著進展,但是隨著電動汽車對熱管理系統要求的提升,熱管的應用目前還存在幾方面問題亟待解決:(1) 動力電池溫度與其動態產熱工況密切相關,進一步的研究應結合實際車用工況,制定有效的實時控制策略,從而實現高效、低能耗電池熱管理。(2) 熱管傳熱方面,由于影響熱管傳熱性能因素眾多,需要綜合考慮熱管內部結構設計及其在電池組中的布置方式,優化其在使用過程中的傳熱性能,特別是針對平板類型熱管的傳熱特性分析及優化設計研究,是將來研究的重點之一。(3) 熱管散熱方面,當前大部分系統設計側重于降低電池組溫升及溫差,較少考慮系統能耗與重量。進一步的熱管強化散熱研究應聚焦于系統多目標優化,綜合系統熱、電特性以及系統能耗和輕量化等指標,提出熱管理系統散熱解決方案。(4) 采用熱管的加熱研究方面,當前的研究大多處于測試并驗證效果階段,進一步研究熱管在不同使用環境下的換熱特性,特別是低溫環境下的加熱策略研究,是將來研究的重點之一。隨著電動汽車的發展,動力電池技術和熱管技術的不斷進步,熱管在電池熱管理中將得到更加廣泛的應用。
標簽:
電源電力 點擊:
版權聲明:除非特別標注,否則均為本站原創文章,轉載時請以鏈接形式注明文章出處。